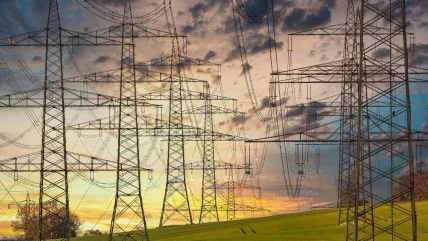
The resistance of traditional high voltage power cables with copper or aluminium conductors causes them to heat up when carrying high currents. This heating represents lost energy. Over long distance transmission the total energy loss can be some 10%. That means the equivalent output of several large power plants is going to waste. Hence the interest in superconducting cables, which offer the enticing prospect of electrical transmission with zero resistance. In fact, a single superconducting cable could carry the combined output of several large nuclear power stations over long distances with no losses within a very compact footprint.
A superconductor has no electrical resistance when cooled below a critical temperature. This ranges from close to absolute zero (-273°C) to -135°C, depending on the specific material used.
Superconductors were discovered as far back as 1911 by the Dutch physicist Heike Kamerlingh Onnes. And the technology has found a number of successful applications in both research and industry, such as particle accelerators and medical imaging devices. However, the potential for perfect power transmission remained untapped for decades, due to the low operating temperatures of the commercially available superconductors. The discovery of high-temperature superconductors (HTS) in 1987 ushered in new prospects for superconducting power applications, focused in particular on fault current limiters, energy storage, and cables for power grids.
Superconducting power cables have gathered increased interest in recent years due to their high efficiency, compact size, and reduced environmental footprint. These advantages are becoming increasingly important as grid operators across the world seek to upgrade and expand their networks to accommodate the transition to renewable energy.
A prominent example of a fully-commercialised installation is the AmpaCity project in downtown Essen, Germany. The 1 km AC cable (Figure 1) is based on high-temperature ceramic superconducting materials.
It is cooled using liquid nitrogen and operates at a voltage of 10 kV and a current of 2.3 kA.
The AmpaCity cable system has been in continuous operation since April 2014.
The installation of this type of superconducting link in inner-city areas can free up valuable space as well as increasing efficiency and lowering operating costs. However, a significant barrier to wider uptake is the high cost of the ceramic- based superconductors because of their complex manufacturing process and limited demand.
A lower-cost superconductor material
In recent years, a promising material has emerged in the form of magnesium diboride (MgB2). This is a simple compound based on raw materials that are abundant in nature. It is easy and inexpensive to manufacture on a commercial basis – making it much cheaper than existing superconductor materials. Most important, it can be readily manufactured into wires for use in power cables. However, these wires are only suitable today for direct current (DC) applications.
Unlike ceramic HTS materials, which are cooled by low-cost and readily available liquid nitrogen, MgB2 needs to be cooled to lower than -248°C. This requires more complex and more expensive cooling systems. The cable is housed in an inner cryogenic envelope cooled by helium gas at -253°C, while an outer envelope is cooled by liquid nitrogen at -203°C, see Figure 2.
There is a trade-off between the cost of the superconductor material and the cost of the cooling system. Currently, MgB2 can be more cost-effective for high voltage direct current (HVDC) projects, but the situation could change in the future, should the production volumes of HTS materials increase significantly, with a corresponding cost reduction.
HVDC superconducting cables
Multi-gigawatt links, more of which are expected to be needed in the future, were the key motivation to study HVDC superconducting cable systems in the European-funded Best Paths project.
An HVDC superconducting cable system is designed to operate at high voltage with a range of possible currents exceeding 3 kA. Below this current level, conventional resistive cable technology is more able to meet grid requirements.
As shown in Figure 3, the HVDC cable system is bipolar, allowing electricity to flow in both directions. Essentially, it comprises these key elements:
- superconductor;
- cryostat (cryogenic envelope), housing the cooling fluid needed to maintain the superconductor temperature;
- high-voltage electrical insulation;
- cryogenic terminations and joints; and
- adequate cooling devices connected to associated power and fluid supplies for the auxiliary equipment such as chillers and pumps.
In addition to the cable itself, the system includes two terminations to connect to the grid and junctions. Depending on the cable length, one or several cooling systems are required along the link to maintain the operating temperature.
Validating a full-size cable system
The Best Paths project focused on validating HVDC superconducting links operating at the multi-gigawatt level. Over four years (2014–2018), a full-size cable system demonstrator operating at 320 kV and 10 kA was specified, designed, optimised, manufactured and fully tested on industrial test platforms.
The 320 kV operating voltage was selected to facilitate insertion into the transmission grid, while the current of 10 kA was the maximum amount achievable by the AC/DC converters. The test programme was guided by recommendations and standards for HVDC cables and accessories.
Best Paths had an extensive preparatory phase, which encompassed the specification, development and optimisation of the main system components. One of the key choices was the selection of MgB2 as the superconductor material, since it had an important impact on the cable design and the choice of the remaining system components.
The superconducting cable was inserted into a cryogenic envelope maintaining the operating temperature along the full length of the link. Flexible cryogenic lines were used as they simplify the cable laying and are commercially available with proven reliability over decades. The final design is shown in Figure 4.
Best Paths aimed to demonstrate the feasibility of an HVDC superconducting cable system able to transmit electric powers higher than 3 GW. Although operating at 320 kV, it was tested at nearly 600 kV in order to meet Cigré recommendations.
A future development, to help keep the overall diameter of the cable as small as possible and therefore minimise its footprint, could be to reduce the operating voltage. The current would then be increased correspondingly to maintain the GW power levels.
Withstanding the quench
The protection of the Best Paths cable system was developed according to the technology and performance of the converters and circuit breakers.
Fault scenarios in the grid were studied to ensure that the cable could withstand accidental conditions, during which the fault current may reach several tens of kA.
For resistive cables, over-current fault management is aimed at avoiding damage to the HV insulation. For superconducting cables, the effort is directed at managing the cable during the fault and its ensuing transition from the superconducting state to the normal resistive state (known as the “quench”).
A fault-tolerant design was adopted for Best Paths. The conductor is designed to withstand the quench, with an over-current during the fault but no damage. The cable has to be disconnected from the grid and can be energised again after the recovery of the operating temperature.
The behaviour of the cable was investigated for an over-current of 35 kA lasting 100 ms. This level of fault current is a representative value required by transmission system operators for a long HVDC cable link.
For the selected Best Paths design, simulations showed that the temperature does not exceed -183°C during and after the investigated fault. However, in general, the value of fault current should be calculated by considering the real grid architecture, in particular, the power available and the impedance of all the circuits connected together.
Practical considerations
Selection of an HVDC superconducting cable must go beyond the technology to consider a number of practical aspects. For example, the cable design should be manufacturable on a large scale over long lengths, with a minimal number of joints. During the installation phases, the cable should be transportable to the different sites along the link, and efficiently laid and buried into the ground. Once in operation, it is crucial that the cable system be robust, reliable, and maintainable.
Realistic solution for bulk transmission
The feasibility and reliability of superconducting AC cables has already been demonstrated and such cables are commercially available. But the European Best Paths project has widened the field of applications by successfully designing, manufacturing and testing a 3 GW class HVDC superconducting cable system.
This shows that superconducting HVDC links represent a realistic solution for bulk power transmission and could contribute to global decarbonisation by reinforcing and increasing the efficiency of electricity grids with very limited environmental impact. If helium gas was replaced by hydrogen as the cooling medium, then superconducting cables would also open up the unique and promising possibility of simultaneous transport of two energy carriers – hydrogen and electricity.
Authors: Frédéric Lesur senior engineer high voltage products and cable systems, Nexans, and Jean-Maxime Saugrain VP machines, cryogenics & superconductors, Nexans
For further information: https://www.nexans.com/business/High-Voltage—Projects/Power-Networks-Land-High-Voltage.html