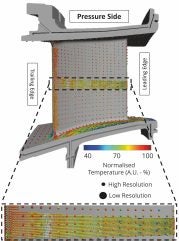
Historically, gas turbine technology development has focused on increasing the turbine inlet temperature and reducing cooling air consumption, to improve performance and efficiency. The cooled engine components, in particular, have become extremely sophisticated with internal cooling channels and arrays of cooling holes across the surface of components. However, the validation of these hot parts by traditional temperature measurement techniques has become more and more challenging and falls short of today’s requirements. The US PIWG (Propulsion Instrumentation Working Group) has, for example, stated that “measurement of surface temperature over 80% of blade airfoil surface for all blades in the turbine is necessary for test monitoring and to verify turbine durability”. Such data is crucial for predicting gas turbine life and maintaining reliable operation.
Sensor Coating Systems (SCS), a start-up located in East London, UK, has been developing thermal history coating technology for a number of years. The results of a collaboration between Doosan Enerbility (South Korea) and SCS were presented for the first time at the 2024 Turbo Expo conference* and attracted a lot of interest from the gas turbine community.
In this world-first study, high-resolution surface temperature mapping, employing thermal history coatings, was carried out for an H class stage 1 turbine vane following long term engine tests.
Thermal history coatings are ceramic-type coatings that are phosphorescent when excited with light. The thermal history coating’s atomic structure permanently changes when exposed to high temperatures and hence alters its phosphorescence properties. This in turn, after calibration, enables the operator to determine the past temperature of the coating at any given point on the component. It is essentially a coating with a temperature memory, which is read out after operation, hence a non-intrusive technique.
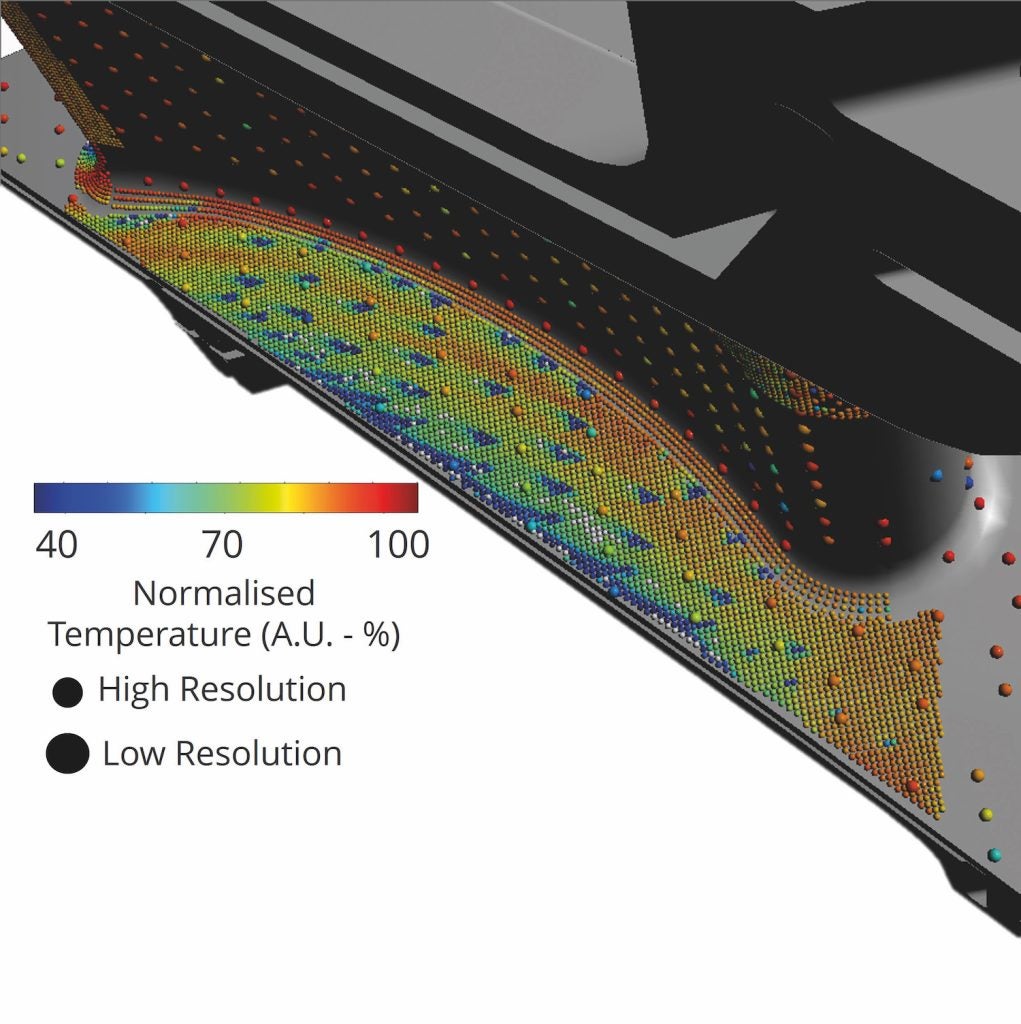
For the Doosan project, the thermal history coating was applied to a nozzle guide vane, which was exposed to a multi-cycle, multi-temperature-level engine test lasting over 8 months. After disassembly of the part, the vane was scanned using SCS’s automated robotic system. During the study, two passes of THC measurements were taken. One was low resolution (LR), with about 1600 measurement points, and the second was high resolution (HR), with an amazing 15 000 measurement points. Point pitches were 5 mm and 1 mm, respectively.
The HR scan provided an unprecedented, unique insight into the maximum temperature profile of the vane, something not achievable with traditional techniques. Particularly around high temperature gradient regions, such as those close to effusion cooling holes, the high resolution scan proved vital as the low resolution scan could not resolve critical features on the component.
The THC temperatures were compared to the engine manufacturer’s (ie, Doosan Enerbility’s) heat-transfer code for validation and has proven to be in extremely good agreement.
The leading edge and pressure side trailing edge regions were typically the hottest. The HR measurements clearly show sharp thermal gradients around the effusion cooling holes on the vane’s aerofoil and platforms.
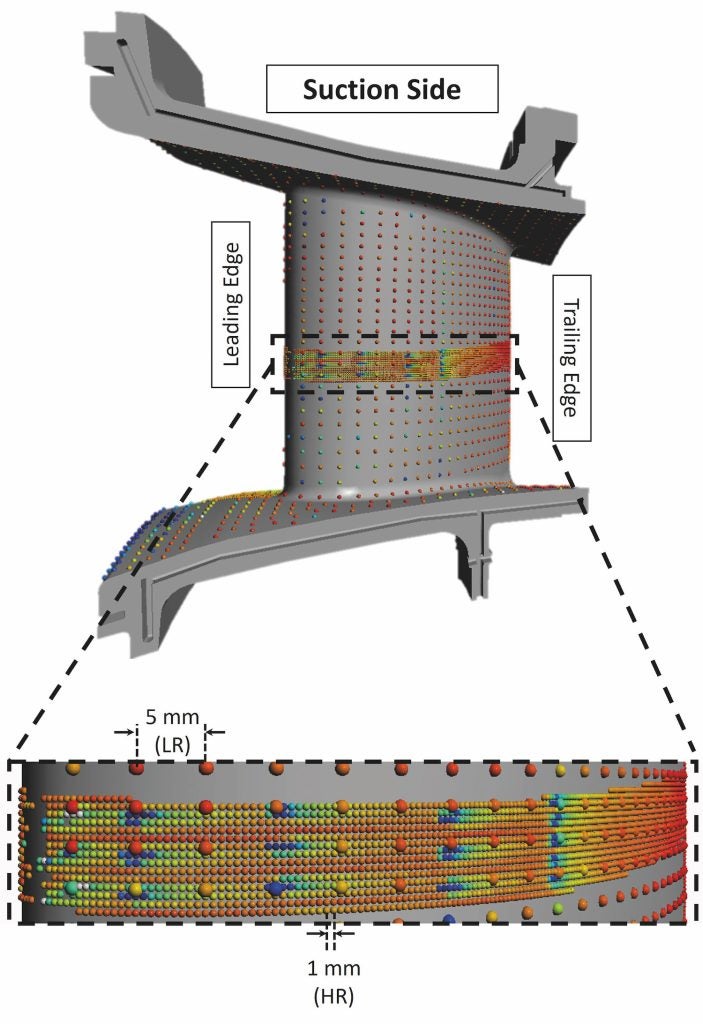
THC based thermal mapping potentially has an important role to play in supporting gas turbine development over the next decade, and will, in particular, be needed to support combustor and turbine designs that facilitate reliable operation on alternative fuels such as hydrogen, ammonia and SAF.
*Proceedings of ASME Turbo Expo 2024, 24-28 June, London, UK. Paper reference number GT2024-126737