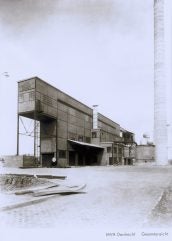
The basic modus operandi for all advanced WtE plants according to the United States Environmental Protection Agency is the ‘conversion of non-recyclable waste materials into usable heat, electricity, or fuel through a variety of processes.’
Collectively, WtE facilities comprise a range of technologies that generate useable forms of energy and byproduct materials from non-recyclable, ‘residual’*, waste produced by humankind that would otherwise be disposed of in landfill sites.
As we will explore, the landfilling of waste has been widely practised over many millennia, but in recent decades we now recognise landfill sites as a major source of damaging greenhouse gases such as methane, nitrogen and carbon dioxide – not to mention the loss of wildlife habitats and the production of landfill leachate, which often damages vital water courses.
As a result, the burying of commercial, household and hazardous wastes is broadly understood to be the least sustainable among modern waste management choices.
For over 90 years Kanadevia Inova has earned its place as a global leader in engineering and WtE advancement, with a strong track record in delivery of turnkey plants and system solutions for thermal, biological and power to gas facilities.
The company was founded in 1933 in Switzerland as L. von Roll Aktiengesellschaft, later known as Von Roll Inova, and in 2010 became part of the Hitachi Zosen Corporation, changing its name to Hitachi Zosen Inova.
The Switzerland-based multinational Kanadevia Inova has over 1600 WtE reference projects globally, which it has built and maintains/operates, a number that continues to grow – even as you read this article.
Burgeoning waste growth, a global problem needing local solutions
To understand the evolution of waste-to-energy over time, we have to identify the way people, society and environmental needs continue to change and, in turn, how these have influenced the way we have treated, and will continue to treat, non-recyclable wastes into the future.
With an overview of how our forebears treated their wastes, we can better understand the origins and development of WtE treatment technology.
Since the first industrial revolution in the 17th and 18th centuries, the global population has burgeoned, with towns and cities needing to grow to accommodate ever expanding and urbanising populations.
Perhaps unsurprisingly, we can simultaneously chart the corresponding growth in the wastes produced per capita over time; together with an increasing volume of waste types produced and discarded over the ensuing centuries.
Most countries and populations have systematically dumped industrial and household wastes into a variety of natural environments including landfill sites, forests, rivers and the open oceans. Today, this is now seen by many governments around the world as unsustainable. International scientific research has proven it to cause untold environmental damage for future generations, all our global environments and continents – including in the Arctic and Antarctic.
However, despite the growing body of scientific evidence, many countries continue to opt to infill any voids available in former quarries, low grade land or natural ground level depressions as large-scale repositories for waste.
By burying material that nearly every human contributes to, the issue of dealing with the ‘refuse of life’ was to put it into landfill where it is then ‘out of sight and out of mind.’
Sadly, according to the World Bank, the practice of landfilling is responsible for about 11% of global methane emissions, produced when organic matter breaks down, creating one of the most aggressive greenhouse gases.
However, whilst landfilling was the solution of choice for many centuries around the world, other countries are restricted or restrained by their natural geography and topography.
For example, excavations in low lying countries such as the Netherlands would quickly hit water, making landfill unfeasible, whilst mountainous nations (such as Switzerland) find their landscape unsuitable or cost prohibitive for landfill sites.
In the 1800s and 1900s, this led to the first commercially sized ‘combustors’, which could burn residual wastes. Whilst these early commercial incinerators were rudimentary by most modern design metrics, they provided a means for waste to be burnt to relieve the mounting civic and public health demands on growing, urbanised societies caused by the waste they produced.
Although early ‘combustors’ reduced the mass of solid waste by 80%-85%, there was little or no pre-sorting of waste before burning. Environmental controls and the monitoring of gaseous outputs were also less stringent at best (when compared with today’s advanced standards), or non-existent at worst.
The combustors of yesteryear admitted all types of waste; non-hazardous, hazardous, bulky and potentially recyclable materials were all ‘treated’ without the need to keep reliable records or origin information on the waste types and volumes. Inevitably, the uncontrolled emissions produced posed major health risks for plant workers, local communities and the wider environment. A better technology solution was needed.
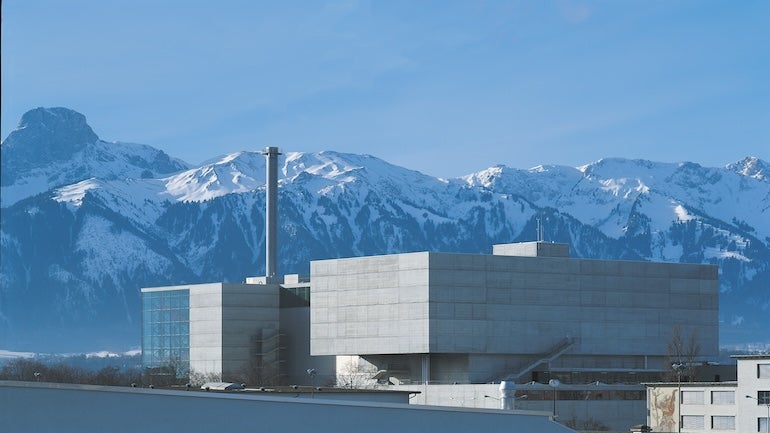
Accelerating the development of WtE technologies
The age of highly designed WtE plants had begun. Tested for robustness and built with proven technologies from the 1960s onwards, more modern WtE plants were now capable of converting the heat produced into electrical energy and/or steam which could be used to power, warm and cool nearby homes and businesses.
In the ensuing decades, these plants went through many design updates and technology iterations, advancing them to be able to safely treat more types of waste, with far greater emission control and more effective flue gas abatement systems.
Today’s WtE facilities can even produce renewable gas and many other benefits, which are now helping to improve our collective environments and combat climate change. Technical innovation, combined with new environmental protection laws and regulation, led the way to today’s highly engineered moving grate WtE facilities. These plants now incorporate significant advances in flue gas cleaning systems, which efficiently scrub noxious post-combustion gases to ensure that each facility fully complies with all applicable operating and environmental requirements around the world.
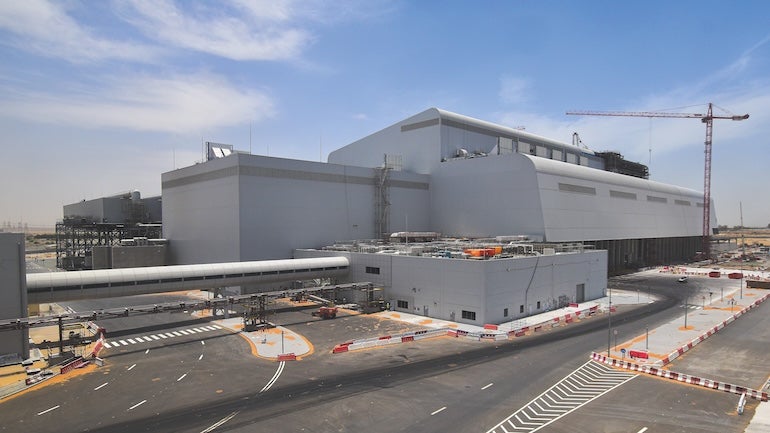
Moving grate WtE technology has enjoyed exponential growth across the globe.
There are multiple drivers behind this demand, but some pre-eminent reasons are based around the moving grate plant’s robust track record, flexibility in handling varying waste types and guaranteed operational availability. This has made moving grate WtE facilities the preferred technology choice for developers and funders of these plants, enabling them to raise the finances necessary to build more such plants.
Over many decades, moving grate WtE plants have proven to be highly durable, and have excellent operational and safety records. This also ensures they provide customers and operational teams with reliable and predictable maintenance schedules and dependable baseload energy outputs.
All told, this makes moving grate WtE technology far more ‘bankable’ than alternative thermal treatment technologies. Many of these alternative thermal treatment technologies have struggled with the technical challenges of upscaling to become commercially viable and reliably capable of treating the shear variety of waste types needing to be processed.
These drivers have seen moving grate WtE facilities become firmly established as the ‘technology of choice’ around the world.
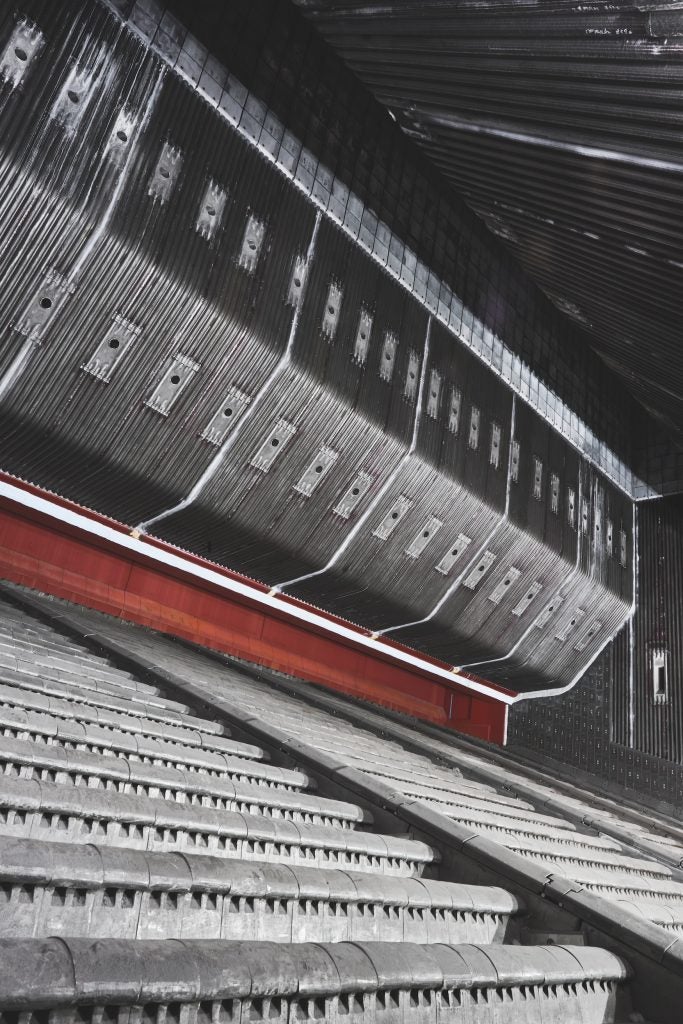
Fit for the future
Kanadevia Inova is, and intends to remain, at the forefront of advanced WtE technologies that meet and exceed the client’s technical expectations, designing and building plants that are fit for the future.
Today’s WtE plants enable residual waste to be used as a fuel for generating large amounts of electricity and/or heat, while metals left after the treatment process, both ferrous and non-ferrous, are recovered efficiently for later reuse.
As well as designing, building and operating new WtE facilities, Kanadevia Inova is also involved in the retrofitting of enhanced flue gas treatment technology and carbon capture systems to existing plants, or new residue handling systems, as well as anaerobic digestion and biogas upgrading.
Kanadevia Inova’s engineers are always researching, developing and acquiring new technologies that can provide proven future solutions and deliver truly sustainable circular economies.
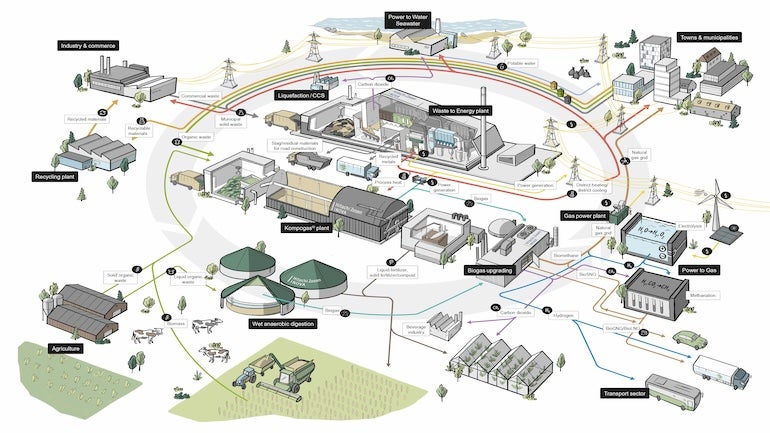
A current focus is on delivering carbon capture technologies, offering customers tailored solutions to meet their specific needs.
Another area of activity is improved treatment methods for the residues from WtE processes, such as recovering more post-treatment metals and other raw materials with the usage of efficient combinations of dry and wet ash extraction to ensure that no waste is ever wasted.
As research and development accelerates WtE technology improvements, key players in this vital global market are confident that WtE facilities will be able to contribute to carbon neutrality in the not-too-distant future.
In the coming years, WtE facilities have the potential to become carbon sinks, actively reducing the volume of CO2 emissions to air compared with the carbon load of residual wastes that are sent for treatment to these plants.
These advancements, in less than a century, demonstrate how far WtE technology has come, from the use of basic ‘combustors,’ to the cutting edge and fully automated plants that are being designed, constructed and operated today.
As already noted, Kanadevia Inova continuously examines the range of technologies and services it offers customers. This constant reassessment allows its engineers to carefully assess whether they can improve plant designs to address specific requirements and meet ever-tightening environmental regulations.
Kanadevia Inova is, for example, working on the development of hydrogen production technologies, including hydrogen liquefaction, biological and catalytic methanisation, and now power-to-gas solutions.
The drivers behind the restless activity of all Kanadevia Inova’s employees are the development and construction of WtE facilities that operate more efficiently and reliably, creating truly circular economies that will benefit future generations.
* Residual waste is the volume of non-recyclable waste that remains after recycling, composting or other waste reduction processes have taken place.