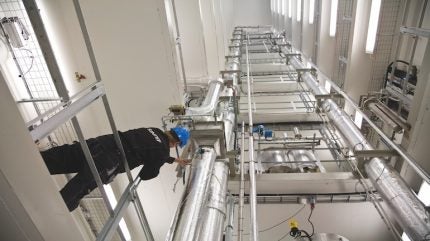
The SINTEF group is one of Europe’s largest independent research institutes. SINTEF Energy Research specialises in originating and advancing innovative energy solutions, with strong foundations in research-based knowledge and industry collaboration, both in Norway and internationally. It has been working on carbon capture for decades. Today, SINTEF conducts research on the whole value chain for CO2 capture, transport and storage for various industrial and power sectors. When the substitution of fossil fuels by renewable electricity is not possible or too expensive, carbon capture and storage (CCS), with CO2 captured from flue gases and placed in permanent geological storage, can speed up the reduction of GHG emissions. In the European research project TRANSITION (grant nr. 101069665), SINTEF is collaborating with research and industry partners (University of Florence, TotalEnergies, Baker Hughes, CERFACS and DLR) to achieve further advancements in carbon-neutral power generation from natural gas fired power plants using gas turbines. To do this, access to a highly efficient carbon capture process is crucial.
When capturing CO2 from the exhaust gases of a natural gas fuelled combined cycle power plant, it is necessary to provide energy to the CO2 capture system, often in the form of heat. This heat is typically taken from the combined cycle process itself. As a result, the overall efficiency of the system is reduced because some of the energy that would have been used for generating electricity is diverted to the CO2 capture process. In other words, finding ways to minimise the energy consumption of the capture process means minimising efficiency penalties. One important factor affecting capture efficiency is the carbon dioxide concentration in the exhaust gas. The higher the concentration gets, the less thermodynamically demanding becomes separation of CO2 from the other gases and the lower the energy requirement for the CO2 capture process.
Typical CO2 concentrations in the exhaust gases of gas turbines are around 3–5% due to low carbon intensity of natural gas and the very high operating air-to-fuel ratio in these engines. A way to increase the CO2 concentration is the implementation of exhaust gas recirculation (EGR). EGR is based on recycling a portion of the exhaust gases to the compressor inlet of the gas turbine, while the remaining part is directed to the CO2 capture system. EGR is a well-established technique in diesel engines for NOx control, but not commercially adopted for gas turbines. Mixing the recycled exhaust gas with air at the compressor inlet results in a working fluid richer in CO2. Another effect of EGR is to reduce the volumes of exhaust gas to be processed by the CO2 capture section, due to the recycle of a portion of the whole gas. Lower volumes translate into smaller sizes for the equipment involved in the capture. As a result, the costs associated with the CO2 capture system decrease, again moving the needle towards more economic operation.
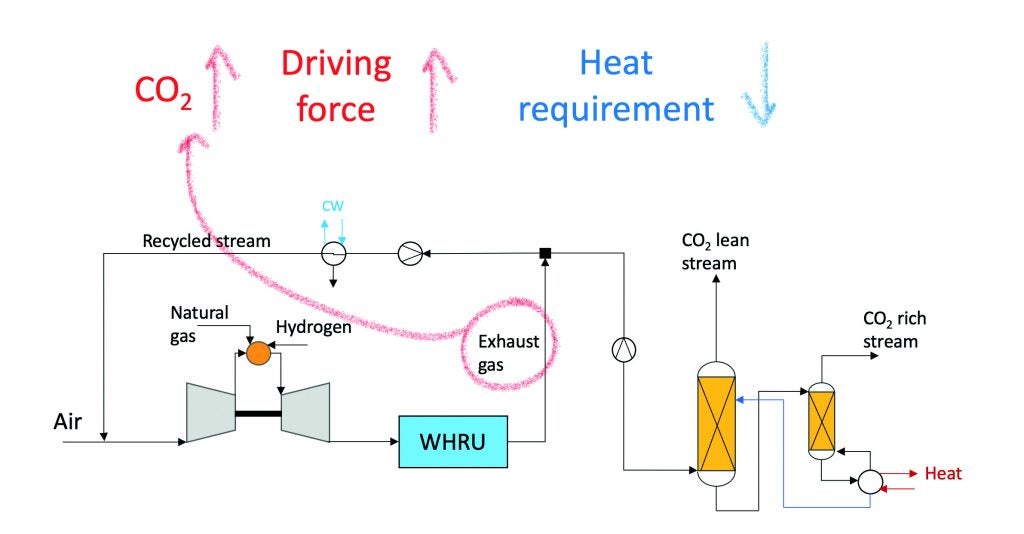
Current status of EGR for gas turbines
Although still not commercially deployed in the gas turbine industry, EGR is a technology add-on that has drawn a lot of attention recently at both research and industrial level. SINTEF has long investigated the concept for the sake of lowering the barrier to capture CO2 from low concentration gases such as in natural gas power generation. Efficiency and cost are of course obvious targets, but in applications with severe space constraints like the offshore sector, decreasing the size and weight becomes an equally important consideration. In the early 2010s SINTEF [1] showed that EGR has the best capability for increasing carbon dioxide concentration with the highest electrical efficiency, compared with other methods for increasing CO2 concentration in the exhaust gas of gas turbines, such as humidification, supplementary firing, and external firing. Actually, with EGR there are further positive side effects, such as a decrease in NOx formation due to lower local flame temperature and a potential for part load efficiency improvement, as shown in the work of the TRANSITION partner TotalEnergies [2], thanks to an inlet air heating effect.
But a major technology bottleneck lies in the combustor of the gas turbine, where it has been established that the amount of exhaust gas that can be recycled is limited to 30-40% before combustion stability and efficiency issues arise, a point already confirmed in the course of GE’s high pressure test facility trials, as reported in 2009 [3].
Challenges and opportunities for EGR
A SINTEF simulation study, in collaboration with TRANSITION project partners from the University of Florence, investigated the impact of exhaust gas recirculation on a natural gas fuelled combined cycle power plant, highlighting challenges and potential. The effect of increasing the EGR ratios (ie, the fraction of the exhaust gas that is recycled) on the downstream CO2 capture process was first assessed.
The CO2 capture technology selected is chemical absorption using monoethanolamine (MEA) as solvent. This is a mature technology, using steam for regeneration of the solvent, widely regarded as benchmark technology.
The results first reaffirm what was already observed in the literature, in that increasing the EGR ratio results in turn in reduced energy penalty and smaller equipment size. In the study, fairly high and impractical EGR ratios (well above the accepted 35-40% limit) were purposely tested. The goal was to investigate whether the positive impact of EGR is attenuating over a certain threshold, irrespective of its feasibility from a combustion perspective. Interestingly, the trends remained stable, seemingly suggesting that: the more EGR, the better. This result means that effort put into further pushing the combustion limit will positively affect the capture plant. And this is the ultimate objective of the TRANSITION project, to investigate hydrogen piloting of the combustor at high EGR ratio. The piloting consists of adding a relatively small amount of hydrogen into the combustor, just enough to maintain stable combustion and allow higher EGR levels. To minimise the amount of hydrogen needed, and its associated cost, clever injection strategies in the burner–combustor arrangement are being developed. The most promising configuration designed by Baker-Hughes and the University of Florence will finally be tested in relevant high-pressure conditions at the partner site DLR, Germany.
Despite the H2 piloting resulting in a small decrease of the CO2 concentration in the exhaust gases, the simulation results show that the advantages derived from increasing the EGR level and stabilising the flame are dominant, with an overall positive impact on system performance. The additional energy penalties of the overall system were also analysed, confirming that the CO2 capture energy requirement is predominant, and that the design of the system should aim at minimising it. As the energy consumption is a key driver of operating costs, and equipment sizes are a key driver of capital costs, these results represent a basis for further techno-economic evaluations.
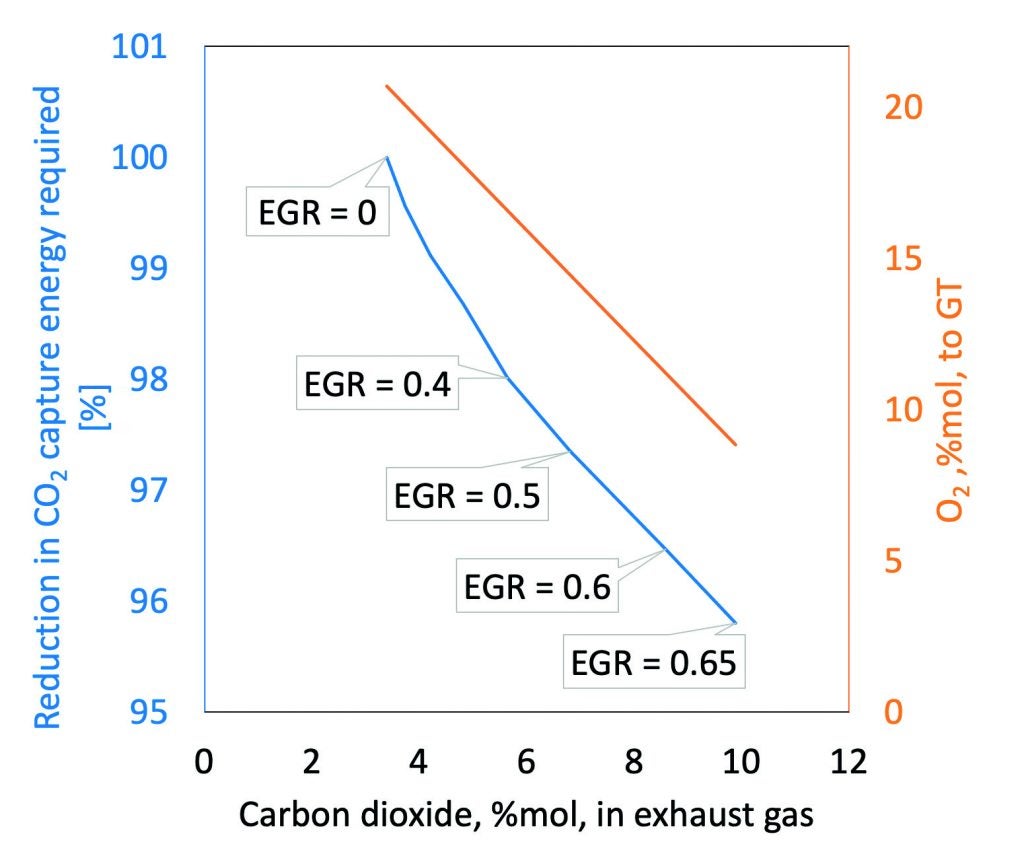
Based on these conclusions, SINTEF aims at focusing its efforts on developing a more efficient power plant with integrated carbon capture and EGR. To achieve this, future steps in the TRANSITION project will include conducting detailed simulations at selected EGR levels, supported by experimental investigation of combustion. This will allow us to further optimise the system and perform techno-economic analyses to explore the feasibility and benefits of optimising exhaust gas recirculation strategies for natural gas fuelled combined cycle power plants.
Although the power sector is going through a radical change where renewable electricity is gradually and inexorably increasing its share, natural gas power generation is expected to continue play an important role in balancing the power system and increasing its flexibility and reliability. Reducing the emissions from natural gas fuelled combined cycle plants is, therefore, a necessity. CO2 capture is currently the lone option available on the table to pursue such reduction. In spite of that, the economic penalties incurred by deploying CO2 capture are slowing down its take up. Exhaust gas recirculation shows substantial promise as a means of improving cost effectiveness but is not yet commercially available. SINTEF, in collaboration with its partners from the TRANSITION project, will strive to further advance EGR towards technological maturity continuing to address remaining limitations via focused research.
References
[1] H. Li, M. Ditaranto, and D. Berstad, ‘Technologies for increasing CO2 concentration in exhaust gas from natural gas-fired power production with post-combustion, amine-based CO2 capture’, Energy, vol. 36, no. 2, pp. 1124–1133, Feb. 2011, doi: 10.1016/j.energy.2010.11.037.
[2] J. Hachem, T. Schuhler, D. Orhon, M. Cuif-Sjostrand, A. Zoughaib, and M. Molière, ‘Exhaust gas recirculation applied to single-shaft gas turbines: An energy and exergy approach’, Energy, vol. 238, p. 121656, Jan. 2022, doi: 10.1016/j.energy.2021.121656.
[3] A. M. ElKady, A. Evulet, A. Brand, T. P. Ursin, and A. Lynghjem, ‘Application of exhaust gas recirculation in a DLN F-Class combustion system for postcombustion carbon capture’, J. Eng. Gas Turbines Power, vol. 131, p. 034505, Feb. 2009, doi: 10.1115/1.2982158.