
Fuel switching to natural gas is increasingly being considered as a smart alternative fuel choice for coal fired plants. Whether the whole plant is converted to burn natural gas, or just part of the plant, there are a number of economic, regulatory, performance, emissions, fuel availability and cost considerations that plant owners and operators should weigh to determine the best solution for their plant and circumstances.
Project drivers – why consider a coal to natural gas conversion?
Regulatory and economic considerations are two of the most-notable drivers in the decision to convert a steam generator from coal to natural gas firing.
Regulations vary widely across the globe and may be driven by international agreements or national, regional or local jurisdictions. Many coal-fired power plants have been slated for decommissioning, and these decisions are often made under the umbrella of reduced carbon dioxide, and other emissions, and effluent regulatory constraints. However, natural gas has been considered as a fossil fuel alternative to coal, offering the potential to utilise the remaining life of some generating assets, while providing fuel flexibility in the electricity generation mix. A coal to natural gas conversion not only lowers the CO2 emissions from the unit, but also typically lowers other air emissions, including particulates, NOx, SO2 and VOCs, and eliminates both effluents from coal flue gas treatment and the need for ash treatment and storage.
The economics of a coal to natural gas conversion is another important consideration. In certain circumstances, the plant operator may find that the conversion makes economic sense, even if regulatory demands are not necessitating the fuel switch. Even with a regulatory need, economic considerations also must be understood, including the expense of bringing an adequate and consistent supply of natural gas to the site and the expected future cost of the fuel versus coal. In addition to fuel costs, natural gas will be of economic benefit as certain environmental controls for sulphur and particulates can be eliminated (as natural gas emits no significant levels of these pollutants). Also, natural gas has inherently lower costs of operation and maintenance, as certain parts of the plant such as coal yards and pulverisers are eliminated, and ongoing wear is minimised as the effects of corrosion and erosion on plant equipment are eliminated.
Fuel availability
The first consideration in determining whether a coal to natural gas conversion is feasible is the availability of natural gas to the site, or the expense of building a reliable and adequate natural gas supply to the site. In the 21st century, investments in natural gas exploration and supply technology and infrastructure have made reliable and low-cost natural gas supplies readily available in many parts of the globe.
In locations where a reliable and low cost natural gas supply is, or can reasonably be, available, the economics of natural gas firing can be favourable in comparison to clean coal.
In making these comparisons, it’s important to factor in not only the coal and natural gas fuel costs, but also the operation and maintenance expenses of the facility, which are notably lower when firing natural gas.
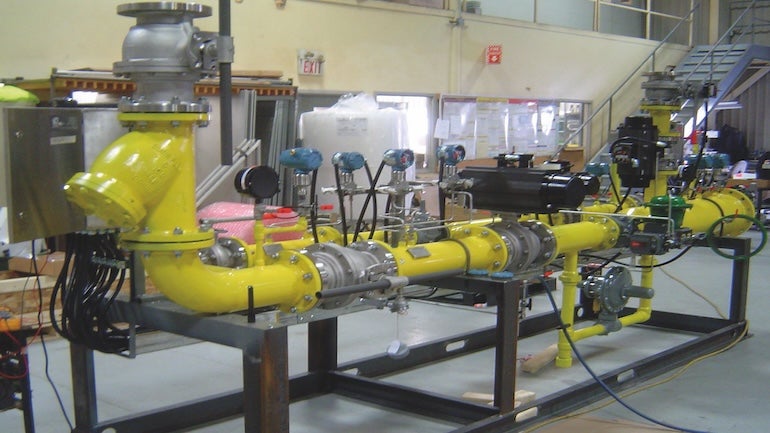
Efficiency and economics
While the firing of natural gas lowers steam generator efficiency in comparison to most coals, the negative impact on plant heat rate can be fully or partially offset by the elimination of equipment utilised in coal firing that consumes parasitic power.
For example, coal pulverisers and ash handling equipment are not required when firing natural gas, and neither are SO2 scrubbers and particulate reducing baghouses. The conversion to natural gas also will result in notable lower operating and maintenance costs for the facility. Maintenance, upkeep and consumable expense associated with pulverisers, ash handing equipment, scrubbers, and baghouses can be eliminated, and ongoing replacement component costs will be reduced as the conversion from coal to gas eliminates the severe erosion and corrosion conditions associated with coal firing and prolongs the life of the steam generator components.
The regulatory environment and economic considerations involved in determining if a coal to natural gas conversion is appropriate are site- and location-dependent. Sites with a readily available or reasonably attainable natural gas supply and regulatory approval often have the necessary drivers in place to justify the conversion.
Performance considerations
Coal is a widely variable fuel composed of differing percentages of carbon, volatile matter, ash, and moisture. These non-uniform characteristics are considered in the design of the steam generator, and associated equipment, and units designed for the same output conditions may be notably different due to the coal characteristics around which they were designed.
By comparison, natural gas is a much more consistent fuel, comprised predominantly of methane (CH4).
While some generalisations can be made when comparing differences in the utilisation of coal and natural gas in a steam generator, each option still must be evaluated on a case-by-case basis, with the specific conditions of the site being considered.
Natural gas also has a clear advantage over coal in terms of lower CO2 and greenhouse gas emissions due to its notable hydrogen component. Heat is generated from the burning of both the carbon and hydrogen components of the natural gas/methane, forming CO2 and water, while the combustion of coal involves the burning of carbon nearly exclusively, resulting in higher CO2 emissions in comparison to natural gas for the same heat output.
However, the water formed in the burning of the hydrogen component of natural gas will vaporise in the furnace of the steam generator, and, as a result, there is a negative efficiency impact. While this efficiency impact is not significant enough to offset the carbon benefits in comparison to coal, the increased heat input while firing gas may have an impact on steam generator performance.
Another differentiator is that coal includes components that are not involved in the combustion process or the generation of heat – notably moisture and ash. The moisture in coal is not driven from the combustion process, but rather is one of the constituents of the fuel. Natural gas has no moisture component in the fuel, nor does it have any ash.
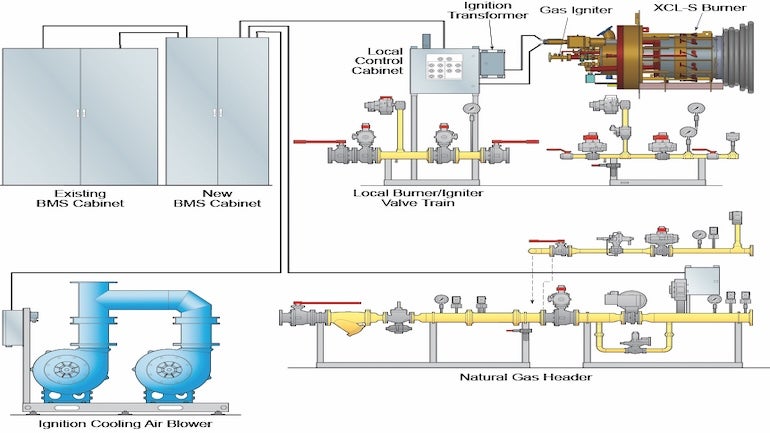
As a result, coal firing has a higher mass flow of flue gas than its natural gas counterpart, and this difference in mass flow may impact the heat transfer in the furnace and in the convection surfaces of the unit.
One means of offsetting this difference is the utilisation of flue gas recirculation – adding increased mass flow in the gas firing case to make it more comparable to the coal for which the unit was originally designed. Another benefit of this approach is lower NOx emissions, as NOx emissions from natural gas can be reduced via flue gas recirculation – a common method of reducing thermal NOx emissions, which are the primary source of NOx when combusting natural gas.
Finally, with respect to the steam generating unit’s performance, a newly designed and supplied gas fired unit will very likely perform differently from an identically designed unit that has previously fired coal. These differences are attributable to the ash and slag accumulation on the unit’s steam generating component surfaces, and their impact on heat transfer. A unit that has been operating and firing on coal for prolonged period will not be as clean as a newly supplied unit.
As a first step in evaluating a coal to natural gas conversion, an experienced and capable engineer should be engaged to evaluate the performance impacts on the unit. Ideally, current operating performance data, the current fuel analysis, and emissions targets should be provided to the engineer, so a thorough unit evaluation can be conducted.
Scope of supply considerations
There are both newly supplied components as well as areas of the existing steam generator that must be assessed for alterations in the typical coal to natural gas conversion.
With respect to newly supplied components, there will be a definitive need for components related to the natural gas fuel delivery system and combustion, or burner, hardware.
With respect to combustion equipment, there are many variables to consider in defining the scope of a coal to natural gas conversion. Most coal fired units were designed for a pulveriser-out-of-service condition, and in the conversion to natural gas for wall-fired steam generators, the number and configuration of the burners should be assessed. In many instances, the total number of burners can be reduced, and the arrangement of the remaining burners can be evaluated for benefits to boiler performance – specifically furnace exit gas temperature. In addition, for both wall and tangentially fired units, emissions are a consideration, as it may be efficient to convert a top burner elevation to overfire air.
If the existing burners are in good condition, with air vanes/burner tilts operable, it may not be necessary to completely replace burner hardware, and the addition of gas nozzles or elements can be considered to modify the existing combustion hardware. If the burners are in poor condition, then a full burner replacement may be prudent.
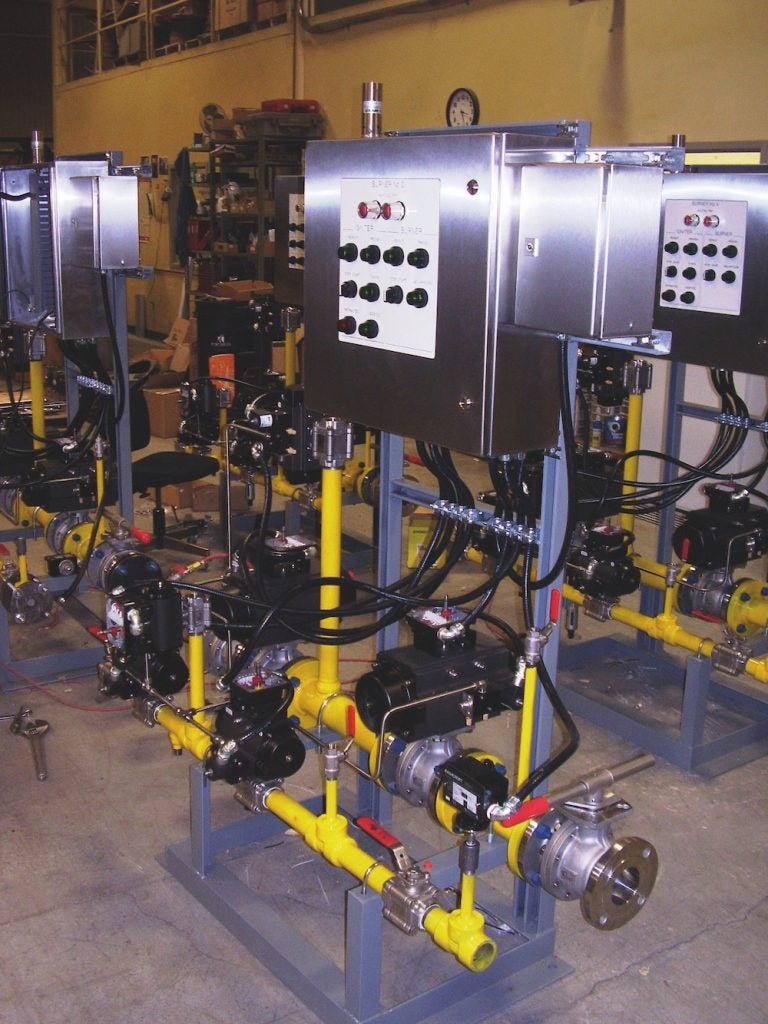
Another critical aspect is the gas supply system to safely provide natural gas to the combustion equipment. These systems typically include pressure regulation and flow-control valves and double-block and bleed pressure relief and venting components.
When considering the scope related to altering existing components, the control system, or DCS, must be modified. Additional control system hardware (including input/output modules) may be required when coal will continue to be utilised, while a complete switch to natural gas may allow the reuse of existing hardware. Older control systems may require updates based on available hardware or requirements of the local jurisdictional authority.
In some instances, burner changes, newly supplied gas supply valve skids and DCS modifications will cover the scope required to allow gas firing. In other instances, efficiency impacts, flue gas mass flow changes, combustion and shifting heat absorption patterns, as well as emissions requirements and air system needs will result in steam generator performance limitations that may be addressed with additional scope.
These changes and alterations may include:
Air supply duct work: In pulverised coal units, some of the air needed for complete combustion of the fuel is provided via the primary air fans, which convey the coal through the pulveriser and to the burners. An evaluation of the existing forced draft fan against the air flow needs and pressure losses through the system post conversion must also be performed. In some instances, the primary air fans may be needed to supplement the existing secondary air fans to provide adequate air flow, and air supply duct scope must be addressed.
Convection pass (superheat and/or reheat) materials and surface: An evaluation of the shifting heat absorption and flue gas mass flows may show that existing superheat and/or reheat metals need to be upgraded to avoid over-stress conditions when operating with natural gas. In addition, the total surface area of these components can be evaluated. If a steam generator is underperforming with respect to steam temperature, the conversion may also offer the opportunity to correct surfaces and restore turbine generator output.
Flue gas recirculation (FGR) fans: Flue gas recirculation may be considered for maintaining gas mass flow and steam generator performance and/or for lower NOx emissions.
Forced draft fans: In some instances, forced draft fans may need to be modified (tipped), or even replaced, to provide the required air flow and static pressures to the converted unit. In the evaluation of draft losses, the decommissioning of sulphur scrubbing equipment and particulate removal baghouses – items that will not be required when firing natural gas – should be considered.
Case by case evaluation
In summary, the conversion of a coal-fired steam generating unit can be considered when an economic natural gas supply can be provided to the site, and when regulatory approvals allow. Many owners and operators of coal-fired steam generators are considering this scenario as natural gas economics can be favourable and CO2 emissions per MW can be significantly reduced.
While natural gas is a very consistent and homogenous fuel, coals are widely varied, as are the impacts relative to the design conditions of the originally supplied equipment. The performance differences between coal and natural gas combustion must be evaluated against the original design and operating characteristics of the exiting unit. Given the wide variability of coals and original unit design considerations, scope needs of the conversion from coal to natural gas must be evaluated on a case-by-case basis and may not only include combustion and natural gas supply components and control (DCS) modifications, but also air flue work, fan and boiler convection pass component metals and modifications.