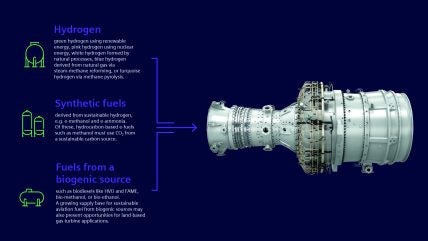
Global warming is a pressing challenge, with GHG emissions having raised global temperatures by 1.1° Celsius since the pre-industrial era. If unchecked, temperatures could rise by 2.9° Celsius by century’s end, causing severe climate impacts and economic burdens. CO2 emissions, largely from combustion of fossil fuels, constitute 67% of GHG emissions, with the power sector and heating responsible for significant portions.
Fossil fuelled power plants currently cover the residual load (ie, the load not met by renewables), but with more renewables in the grid, the residual load will fluctuate daily and seasonally even more. There will also be “dark doldrum” events lasting weeks, as seen in Germany in January of 2017, and climate change may extend these events. Importing electricity can help, but similar weather conditions will affect neighbouring regions simultaneously, and long-distance HVDC connections – even in ideal conditions – won’t fully address the issue.
Demand-side management (DSM) can reduce the load gap, but it’s limited by its scale and duration and the need for the right conditions and pricing to be in place to determine consumer behaviour. Energy storage technologies such as batteries and pumped hydro can cover a range of timescales, but are not feasible for long periods or even seasonal storage of energy. Therefore, efficient, decarbonised, and flexible gas turbines are an essential prerequisite for the future energy system.
Due to their fuel flexibility, gas turbines are pivotal in the transition because they’re capable of using biogenic, synthetic, and carbon-free fuels or fossil fuels with CC(U)S. Siemens Energy is actively developing technologies for decarbonisation across various fronts.
In an energy system with a large share of intermittent renewables, power shortfalls for heat pumps and electric furnaces may occur, especially during winter in high-latitude regions. Gas turbines and CHP plants can bridge these gaps by utilising hot-water heat storage to decouple power and heat production. By following the electricity market and supplying heat, CHP plants offer high energy utilisation rates, up to 90%, making them efficient for both residual load and heat demand coverage.
To achieve either full gas turbine decarbonisation or carbon neutrality, two main transformation routes appear to be feasible: operating gas turbines on decarbonised or carbon-neutral fuels; or continuing to operate them on fossil fuel, such as natural gas, with CC(U)S.
Sustainable gaseous and liquid fuels for gas turbines
Hydrogen
Hydrogen is gaining traction for power sector decarbonisation, with all manufacturers aiming for 100% H2 gas turbine capability by 2030, and some OEMs, such as Siemens Energy, releasing selected H2-capable frames earlier. Technical challenges include hydrogen’s combustion properties, notably lower ignition energy and higher flame speed. Sustainable hydrogen production methods range from renewables and nuclear energy powered electrolysis (green and pink H2) to natural gas with CCS (blue H2) or pyrolysis (turquoise H2).
The EU-Horizon-2020-supported HYFLEXPOWER project demonstrated renewable-power-to-H2-to-power at a cogeneration plant in France employing an SGT-400 gas turbine equipped with dry low emissions (DLE) combustion technology. Successful operation was demonstrated at 100% H2 – a world first for an industrial gas turbine of this size (>10 MW).
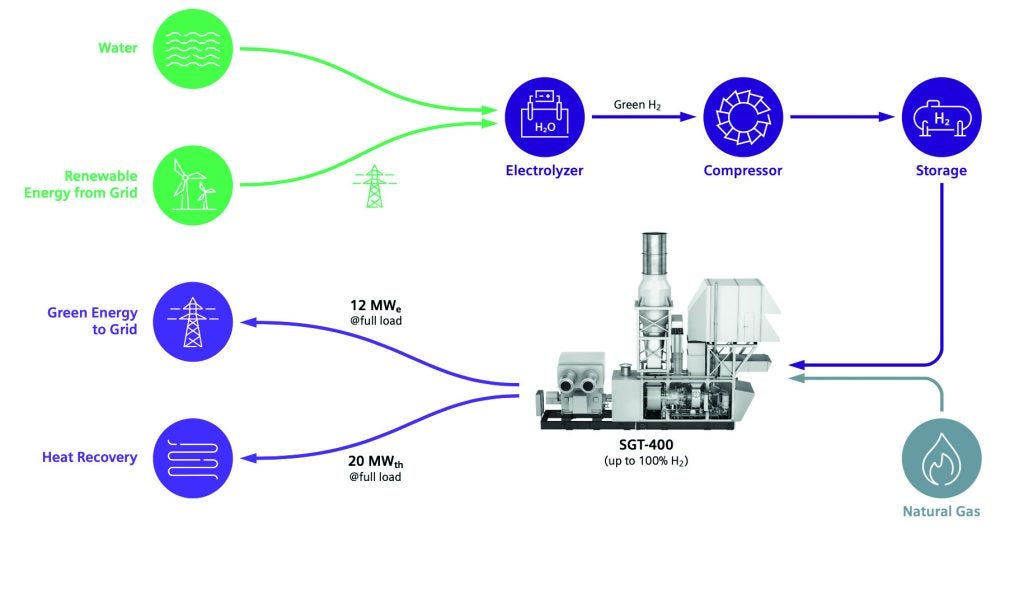
Biogas
Biogas produced from organic matter decomposition typically contains 40 to 75% methane along with CO2 and other minor contaminants. It has a relatively low heating value, making it suitable for small to medium gas turbines. Incentives for using biogas to fuel gas turbines include reducing CO2 and CH4 emissions from natural decay, although gas pre-processing and biomass transportation lead to additional costs.
Renewable natural gas
Renewable natural gas (RNG), or bio-methane, is pipeline-quality gas compatible with gas turbines. It’s made by purifying biogas or gasifying dry biomass such as wood waste and then methanating the resulting H2 and CO. RNG’s use is cost-driven, with incentives like tax breaks and renewable certificates for its distribution and use.
Synthetic methane
Synthetic methane, also known as e-methane, is created by methanating H2 and CO2. It can be utilised in gas turbines without modifying them. It has the lowest carbon footprint when produced from green H2 and biogenic CO2 or CO2 derived from direct air capture, and it can even enable carbon-negative operations with CCS. E-methane is anticipated to be used primarily in chemical processing, while gas turbines are likely to opt for green H2 or easier-to-handle hydrogen derivatives like e-methanol.
Sustainable liquid fuels
Sustainable liquid fuels are also an alternative for gas turbine operation. These include biodiesels, hydrotreated vegetable oil, fatty acid methyl esters (FAME), and Fischer-Tropsch diesel. Most of these fuels are already certified for use in gas turbines, eg, Siemens Energy’s SGT-800 can already run on 100% HVO.
(Cracked) ammonia
Ammonia can be easily liquefied and has a higher energy density than hydrogen, making it practical for storage and transport. However, ammonia combustion in gas turbines isn’t well advanced due to challenges such as high NOx emissions and the need for more safety measures to eliminate the risk of ammonia exposure.
Cracked ammonia offers a promising path to overcoming certain ammonia combustion challenges by using hydrogen as a reactivity promoter. Siemens Energy’s SGT-800 can already co-fire using cracked ammonia, and fully cracked ammonia will likely emerge as the long-term preferred option for ammonia electrification. While site-specific techno-economic factors vary, countries like Germany may import hydrogen as ammonia, and major EU shipping terminals may be potential sites for centralised ammonia cracking and transport via a hydrogen pipeline network.
Methanol
Methanol is primarily a chemical industry feedstock, and it’s being increasingly sought out as sustainable bio-methanol or e-methanol from green/blue hydrogen and sustainable CO2. It offers a much higher energy density than hydrogen. The CO2 can be derived from direct air capture as well as diverse biomass and waste sources. It will become increasingly available to sectors like shipping, and is compatible with the existing infrastructure for storage and transport. With its considerable potential for direct gas turbine use, methanol applications range from base load power to backup for data centres and island grids.
Ethanol
Bioethanol is the most common biofuel. It’s produced from sugarcane or corn, but these first-generation sources aren’t considered sustainable due to competition with food production. Second-generation bioethanol that’s made from waste biomass or biomass produced on land not suitable for food production avoids this issue. Ethanol demand is policy-driven for vehicle fuel blends, but with increasing electrification of transportation, its use in gas turbines may grow. However, e-methanol is simpler to synthesise and so it’s more likely to be used for gas turbine applications.
Dimethyl ether
Dimethyl ether (DME) is a clean, non-toxic synthetic gas that’s used as an aerosol propellant and in the chemical industry. It has the potential for gas turbine combustion due to its high cetane numbers and complete burn, which reduce emissions like NOx and SOx. However, its use in turbines may require fuel system modifications, and there are concerns about supply availability and safety due to gasification upon leakage. As methanol is often an intermediate compound in DME synthesis, it is usually more beneficial to use methanol directly and avoid the additional processing steps which only add additional costs and energy losses. Methanol is also much easier to handle, transport, and store. DME may, however, be a fuel of choice for locations where it is available in sufficient quantities and where its conversion to electricity makes sense.
Integrating carbon capture
The integration of carbon capture with gas turbine power plants can be achieved via pre-combustion capture, oxyfuel firing, or post combustion capture (absorption and adsorption).
The relatively low CO2 concentrations in gas turbine exhausts present a challenge for post combustion capture that may be addressed by exhaust gas recirculation and/or development of novel technologies.
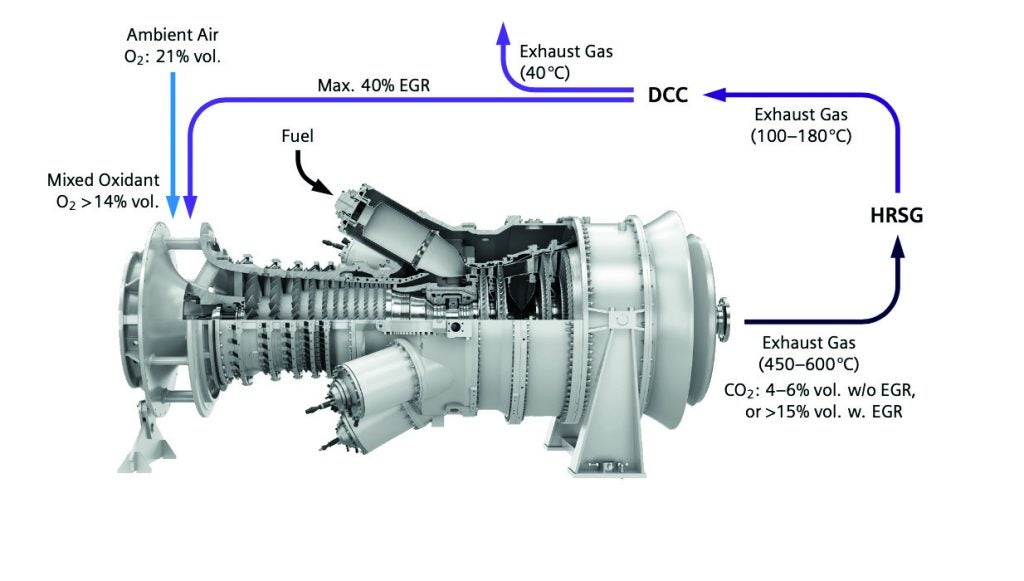
As with the other decarbonisation pathways, techno-economic factors (eg, the plant efficiency penalty due to steam consumption in amine based post combustion capture (PCC)) will determine how widely carbon capture is adopted.
Siemens Energy is supporting the development of carbon capture for gas turbines today by focusing on integration of the carbon capture plant with the gas turbine power plant and carbon dioxide compression.
Mature amine solutions are currently ready for deployment and incentivisation schemes implemented by governments around the world are generating accelerated interest in the deployment of gas turbines with carbon capture.
Many companies are looking at the development of advanced carbon capture technologies, with improved amine processes, alternative solvents and solid sorbents seen as promising future technology steps.
Potential pathways
Decarbonisation strategies vary regionally, and the most economic and beneficial solutions are influenced by location, fuel prices, and infrastructure development. Diverse technical solutions and continued R&D, partnerships, and full supply-chain consideration are crucial for successful decarbonisation, with green hydrogen, ammonia, methanol, biofuels and carbon capture as potential pathways.
*The complete white paper can be downloaded here