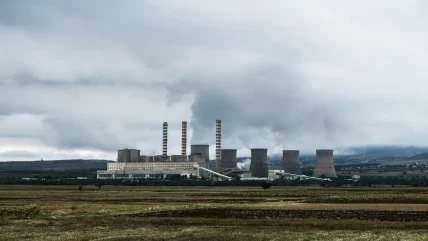
The challenging European objectives of decarbonising the energy sector and the growing urgency to achieve greater energy independence is driving research and development in two directions: reducing the environmental impact of fossil fuel based technologies; and replacing these technologies with carbon free power generation systems.
In the most energy-intensive industrial sectors, such as petrochemicals, but also cement, glass and steel, the use of alternative technologies, such as the recovery of waste heat otherwise exhausted to the atmosphere, can produce both economic savings and a reduction in carbon footprint. This is why, especially in highly industrialised countries, there’s growing interest in exploiting not only the noblest heat sources, thermodynamically speaking, ie, those characterised by high energy content and high temperature, but also those flows with lower temperature and lower enthalpy content, which inherently would have a lower conversion efficiency. These latter flows need technologies that can be economically sustainable with a low upfront investment.
One possible approach is the use of ORC (organic Rankine cycle) systems, which, although based on the traditional Rankine cycle, use a fluid or mixtures of organic fluids of various kinds within the cycle. Thanks to this peculiarity, the choice of fluid used allows the exploitation of thermal resources with a range of thermodynamic characteristics.
Exergy’s ‘Smart ORC’ R&D project
To meet the technical and economic requirements for ORC systems suitable for the recovery of thermal waste at low temperatures, Exergy, in collaboration with Regione Lombardia and the EU, successfully participated in the “Tech Fast Lombardia” call for proposals of the POR FESR (Programma Operativo Regionale del Fondo Europeo per lo Sviluppo Regionale 2014-2020) co-financed by the FESR.
Exergy’s project was called “Smart ORC” and involved the development of a family of “mini” (less than 1000 kW) and “micro” (less than 100 kW) modular ORC systems with very high efficiency, building on the company’s proprietary technologies.
Thanks to the involvement of the Politecnico di Milano and local manufacturing companies in the detailed design and construction of the most critical plant components, an ecosystem for the development of further high-efficiency ORC systems and turbomachinery, both turbines and compressors, has been created.
The production of electricity employing ORC technology can be regarded as a form of distributed generation, and with the ability to input waste heat to the cycle as well as to meet the production site’s own consumption, ORC systems have the flexibility of being able to feed into the grid, self-consume or store the energy produced (in electrical or thermal storage systems).
In current small ORC systems, volumetric turbines, eg, screw or vane, or small centripetal radial turbines are used. Both these turbine types are characterised by lower isentropic efficiencies than those recorded for larger ORC based power plants equipped with radial outflow turbines.
If volumetric machines typically have lower peak efficiencies than turbomachinery, settling at values of around 60-75% (isentropic total to static), centripetal radial turbines are penalised by the difficulty of having to dispose of the entire enthalpy jump in a single stage and, consequently, suffer from limited efficiency.
The adoption of the Exergy radial outflow turbine (ROT), Figure 1, a technology covered by several patents, has many advantages:
- concurrent combination of fluid expansion and increased cross-sectional area;
- mechanical components designed to be easily removable, without the need to empty the system, reducing maintenance times;
- extended bearing life due to very low vibration;
- reduced rotor leakage and friction; and
- greater freedom of choice of both pressure levels and stage pressure gradient, limiting vortex formation and reducing fluid dynamic losses.
Overall, it is a more efficient and reliable turbine technology, with low vibration levels and less noise.
The range of sizes of standard ORC modules investigated and developed in the course of the Exergy Smart ORC project has been selected to suit a wide spectrum of possible heat sources available in the industrial world: 80 kWe; 160 kWe; 210 kWe; 450 kWe; 600 kWe; 850 kWe (gross electric power).
The refrigerant R1233zd(E) is employed as working fluid.
For these capacities, modular, compact and standardised technology enables, on the one hand, faster installation, construction and reduction in overall system costs, and on the other hand, with the selection of a specific working fluid, promises high performance in compliance with the necessary requirements of safety, non-flammability and low environmental impact.
The resulting low mass and volumetric flow rates, which are considerably lower than those found in medium and large size ORC plants, required some adjustments to the ROT turbine, the component with the highest level of what might be called technological content.
The new machine was therefore scaled down to a smaller size, with higher rotational speeds, than the reference ROT turbine, in order to maintain its high performance.
The high rotational speeds required (up to about 20 000 rpm) led to the development of specific methodologies for modelling and performing calculations for ‘fast’ rotors, as well as the design and manufacturing of vibration reduction systems known as SFDs (squeeze film dampers), see Figure 2, typically used in the aviation industry on commercial and military engines, to stabilise rotors operating at high rotational speeds. The great usefulness of SFD systems lies in their dampening effect on the machine.
Also, the pressurised oil chamber employed in the new machine and its fixed anchorage to the bearings provides a considerable further reduction in vibrations, which are exacerbated by the destabilising action of the rotor’s sealing labyrinths, designed to contain the fluid during its expansion.
In addition to the rotational issues, it was necessary to adopt a speed reducer for the mechanical coupling to the electric generator. While the efficiency of the turbomachine is a function of blade rotational speed, typically the generator has a rotational speed determined by the number of poles it has and the frequency of the electricity grid to which it is connected. A ‘slow’ generator is preferable to a ‘fast’ one due to efficiency losses in the machine itself and in the frequency converter (inverter) needed at high frequencies. With the aim of limiting transmission losses between the turbine and generator, a straight-tooth, seven-satellite, low service factor planetary type gearbox was selected, manufactured, and fully integrated into the new machine.
Family of Smart ORC modules
Following the promising results obtained on the test bench, through the R&D project described above, Exergy has acquired the necessary know-how to propose a family of Smart ORC modules plus associated development of small and standardised turbomachinery. This broadens application of Exergy’s radial outflow turbine to very small (micro and mini) ORC systems for electricity production from such sources as diesel engine exhaust systems and waste heat available in several industrial processes.
Application of the R&D to date is expected to increase the efficiency of mini and micro ORC systems by about 5 to15%.
Author: Silvio Meletti project engineer, Exergy International srl, Italy