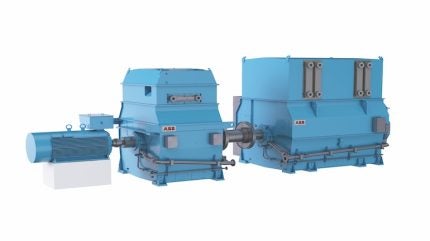
The need to decarbonise power production and increase the use of renewable energy has led to rapid changes in the way power is generated. Almost without exception renewable power sources are “non-synchronous”, with inverters connecting to the power grid. These inverters have no inherent kinetic reserve. At the same time, large fossil fuelled power plants are being decommissioned, and with that the total spinning mass or kinetic reserve in the power system is reduced.
The rationale for developing flywheels for use in synchronous condensers derives from these major changes occurring in the power system. More renewables lead to less inertia, less fault current contribution and the risk of more power oscillations and less damping. It is therefore no surprise that the wish to increase the kinetic energy of synchronous condensers with the addition of flywheels is creating a drive for bigger and bigger flywheels to become available on the market.
For ABB this is not just about increasing flywheel inertia. Security and reliability come first, and with that, an increased focus on safety and failure mode effect analysis as well as tougher requirements for auxiliary systems and for the balance of plant equipment.
We want to make sure that our plants fulfill safety requirements not only today, but also after ten years of operation. The losses associated with our flywheel solution are a bit greater than those experienced with vacuum chamber flywheels, but, for ABB, safety is paramount and therefore our preferred technology is synchronous condensers with flywheels located in integrated safety enclosures.
ABB´s whitepaper Ensuring the safety of large flywheels used to stabilize electrical networks* aims to make users of synchronous condensers with flywheels aware of the lack of specific standards covering these machines.
The consequence is that safety measures need to be handled by the supplying manufacturer and the owner of the plant. Unfortunately, only ISO norm ISO12100:2010 is applicable to the safety of this type of machinery, setting out general principles for design, risk assessment and risk reduction. For the US market a Recommended practice for the design and operation of flywheels has been written by Sandia National Laboratories (SAND2015-10759).
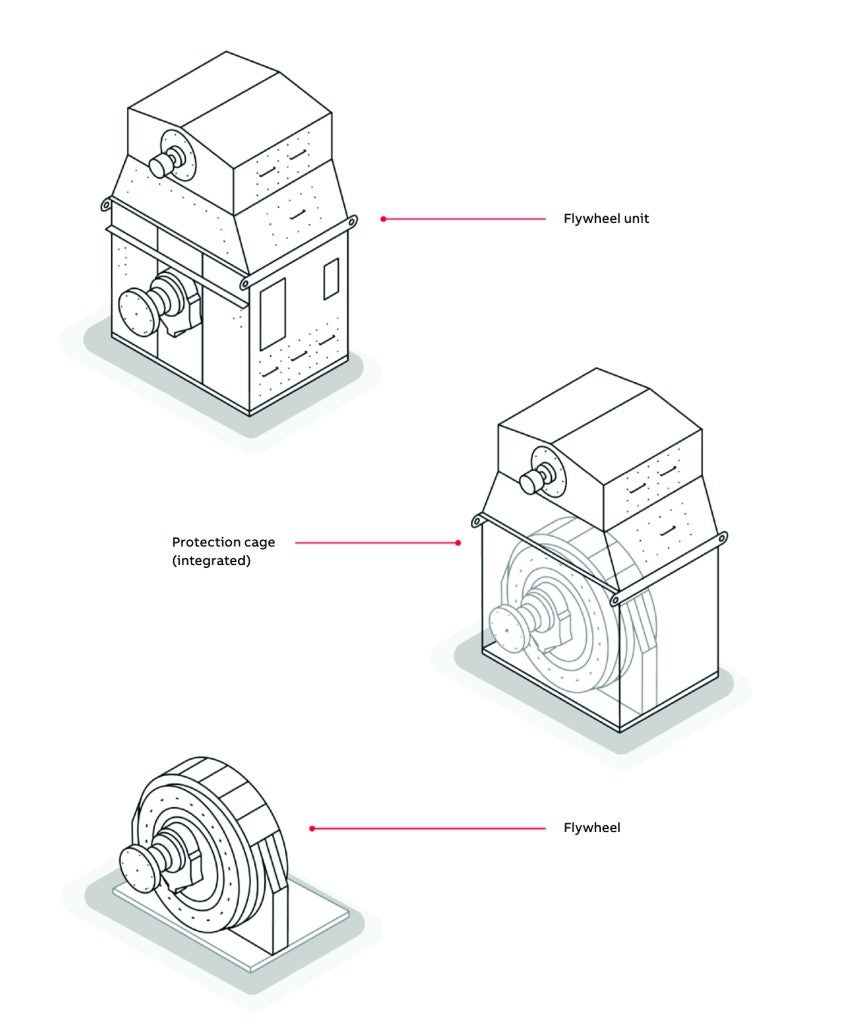
The ABB white paper describes the basic principles of flywheel risk assessment. Even though the probability of a crack in the rotor or the flywheel is very limited, the severity and consequences of such a failure can be significant.
The white paper describes the principles of safe design as well as recommended practices and how they are to be implemented. It concludes with a description of a proposed design for a flywheel for synchronous condenser applications.
The recommendations summarised in the white paper provide the basis for the flywheel design used in ABB’s ongoing supply and delivery of flywheel-equipped synchronous condensers.
ABB’s recent synchronous-condenser-with-flywheel experience includes the following projects:
- Lister Drive 1, 67 MVA, 470 MW.s (UK);
- Lister Drive 2, 67 MVA, 470 MW.s (UK);
- Santa Ponsa 1, 55 MVA, 468 MW.s (Spain);
- Santa Ponsa 2, 55 MVA, 468 MW.s (Spain);
- Jares, 28 MVA, 468 MW.s (Spain);
- Arucas, 28 MVA, 468 MW.s (Spain);
- Drago, 28 MVA, 468 MW.s (Spain);
- Darwin, 40 MVA, 465 MW.s (Australia); and
- Jeju Island, 50 MVA, 497 MW.s (60Hz) (South Korea).
Author: Christian Payerl, Area Sales Manager, Synchronous Condensers, Europe and Australia, ABB