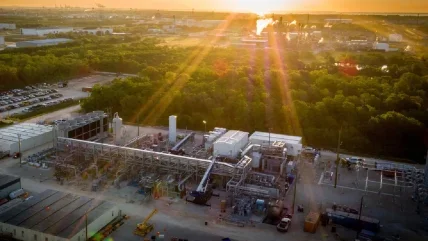
The Allam–Fetvedt cycle enables thermal power generation from fossil fuels with zero CO2 emissions to air. It uses supercritical CO2 (sCO2) from oxyfuel combustion as the main working fluid in a semi-closed Brayton cycle. sCO2 is also at the heart of the indirect-fired supercritical CO2 recompression Brayton cycle that can be used with concentrated solar power, or on modern nuclear reactors. Gaseous CO2 can also be used as a working fluid in reversible power storage cycles to complement non-programmable renewable power generation.
sCO2 as a working fluid in the Allam–Fetvedt cycle
The Allam–Fetvedt cycle can enable the use of gasified coal or natural gas to contribute to a net-zero future. It offers high-efficiency power generation from traditional fossil fuels in an innovative cycle that avoids greenhouse gas emissions. The process relies on oxy-fuel combustion, which also ensures that pollutant emissions are avoided and enables post-combustion CO2 to be captured at high pressure and low cost.
As in conventional air-fed, gas-fired turbines, combustion gases spin the main turbine in the Allam-Fetvedt cycle. However, in the Allam–Fetvedt case, they consist of a mixture of approximately 97.3% CO2 and 2.7% water.
Supercritical CO2 is recirculated within the Allam–Fetvedt cycle as the main component of the working fluid for power generation. Transfer of heat from the hot turbine exhaust gases to the burner inlet gases is essential to achieve efficient operation of the cycle. Printed circuit heat exchangers have been used for this application to combine high efficiency and process intensity.
The main turbine for the original Allam–Fetvedt cycle demonstration facility at La Porte, Texas, was built by Toshiba. Recently, Baker Hughes has taken on the role of turbine development and production for future deployments of the Allam-Fetvedt technology.
The temperature and pressure mean that the CO2 is supercritical at the turbine inlet. And the presence of moisture means that carbonic acid formation is possible. Materials selection and coating technologies are the key to successful turbine operation in this environment.
Post-combustion CO2 capture generally takes place at the end of a power generation combustion process where the gas stream is very low pressure, and the CO2 is often diluted with nitrogen from combustion air.
One of the challenges of this mode of post-combustion CO2 capture is the low-pressure flue gas stream requires a very large CO2 absorber tower to handle the high volume of low-pressure flue gas. Additionally, a large CO2 compressor is required to blow the captured CO2 away to a suitable sequestration location.
Pre-combustion CO2 capture (for example in steam methane reformers that are used for hydrogen production) can take place at high pressure and high CO2 concentrations, thereby reducing the capital and operating costs of CO2 capture. Uniquely, the Allam–Fetvedt cycle enables low-cost, high-pressure, post-combustion CO2 capture because CO2 is released from the cycle at about 80 bar. This avoids the need for CO2 compression.
Furthermore, pure CO2 is released directly from the Allam–Fetvedt cycle avoiding the need for CO2 capture equipment to separate the CO2 from nitrogen, oxygen, and other typical flue gases.
And, since there is no other route out of the process for the CO2, the CO2 capture rate from the Allam–Fetvedt cycle is very high, about 100%.
Supercritical CO2 in the recompression closed Brayton cycle
Sandia National Laboratories, Albuquerque, has researched and demonstrated a supercritical CO2 recompression Brayton cycle and dispatched around 10 kW of power to the Sandia–Kirtland Air Force Base electrical grid for 50 minutes during a test in August 2022.
At a larger scale, the US DOE-funded STEP Demo project will see the operation of a 10 MWe power plant using similar technology (see Modern Power Systems, Nov/Dec 2023). This plant will be the world’s largest indirect-fired sCO2 power cycle test facility and will use a recompression closed Brayton cycle (RCBC) with sCO2 as the working fluid.
Like the Allam–Fetvedt cycle, high efficiency heat exchangers and robust turbines are the key technology components in the indirect-fired sCO2 recompression Brayton cycle and these are two of the main research areas within the STEP programme.
Supercritical CO2 based power cycles have the potential for increased heat-to-electricity conversion efficiencies. As a power generation working fluid, sCO2 combines the best properties of both a liquid and a gas because it has a high density and low viscosity. The sCO2 remains in the closed system and is not released as a greenhouse gas. It is an advantage that sCO2 can operate at up to 700°C – a much high temperature than steam.
A large amount of energy is lost when steam turns back into water in the Rankine cycle. The implication is that only one third of the energy in the steam can be converted into electricity. In comparison, the sCO2 Brayton cycle has a theoretical conversion efficiency of more than 50%. The RCBC has the potential to be significantly more efficient than the traditional steam-based Rankine cycle because sCO2 can operate between low and high temperatures and low and high pressures without a phase change.
Unlike the Allam–Fetvedt cycle, fuel combustion takes place outside the RCBC since it is an indirectly heated process. The RCBC therefore has the flexibility of being fuel agnostic, but if CO2 is generated by fossil fuel combustion, the resultant CO2 would need to be captured to yield climate-neutral power generation.
Supercritical CO2 as a working fluid offers high power density and simplicity of operation compared to a steam-based power cycle and can use more compact turbomachinery. This makes the cycle relevant to a wide range of applications in addition to power generation from nuclear, fossil, geothermal and concentrated solar heat sources. For example, the sCO2 power cycle can be used for maritime propulsion and waste heat recovery.
Supercritical CO2 as a working fluid is also being considered for advanced nuclear reactors. When compared to the helium Brayton cycle, sCO2 has the advantage of lower temperature operation. To achieve a similar heat to power conversion efficiency, helium would need to be heated to circa 850°C, whereas sCO2 is required to be heated to around 550°C. sCO2 can therefore be applied to nuclear reactors with a core outlet temperature above 500°C.
Gaseous CO2 cycle for LDES and grid balancing
The Italian startup Energy Dome uses subcritical gaseous CO2 in a closed cycle in its CO2 Battery™ (see also page 25). The technology is a form of long duration energy storage (LDES) that avoids the use of conventional batteries. The Energy Dome cycle expands vaporised liquid CO2 across a turbine to generate power during periods of peak demand, typically overnight and in the early morning when power is drawn from the grid before solar generation has begun.
The expanded CO2 is stored in a large dome at atmospheric pressure.
When there is abundant renewable power generation from solar PV sources during the peak daylight hours, CO2 gas is withdrawn from the dome. It is compressed and liquefied using excess power from the grid which may otherwise be curtailed. Heat energy from the compression is stored in a thermal energy storage system. This heat is subsequently used to revaporise the liquid CO2 to ensure maximum cycle efficiency. The whole cycle operates below the triple point of CO2, avoiding supercritical operation.
Energy Dome has developed a standard design that produces 20 MW of power over a 10 hour discharge period. The charging time is 10 hours, which can match well with the solar excess period in many renewables-led grids. The duration of discharge is longer than most battery systems can offer and is a complementary fit to solar-heavy grids. Excess solar generation is increasingly common in areas with a high percentage of rooftop solar generation, such as South Australia.
Furthermore, green hydrogen systems based on solar power without overnight wind power integration may benefit from the Energy Dome for overnight power to the electrolysers to ensure high utilisation and avoid periods of shutdown. The daily cycling of the Energy Dome system is also a good fit to the LDES business model, which relies on high utilisation of the capital asset to ensure maximum revenue generation with frequent charging and discharge cycles. Revenue can also be generated through grid management services and excess power withdrawal to avoid power surges on the grid.
Low-pressure CO2 storage is an integral aspect of the Energy Dome concept. The amount of CO2 gas that is stored determines the amount of power that the CO2 Battery™ can release on demand. To enable low-cost storage of a large volume of CO2 gas at close to atmospheric pressure, Energy Dome can use the concept developed by another Italian company, Ecomembrane.
The Ecomembrane technology relies on a PVC-coated polyester fabric membrane. This material has been used for decades as a low-cost means to contain biogas in wastewater treatment plants and store recovered landfill gas. The Ecomembrane has been used on more than 1000 installations around the world for these purposes.
Author: Stephen B. Harrison, sbh4 consulting, Germany