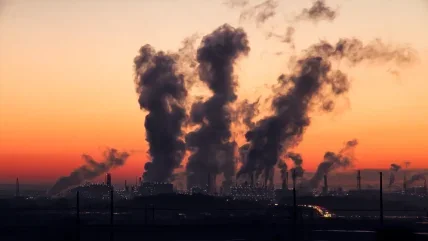
In recent years, large combustion and waste incineration plants around the globe have had to cope with a series of regulations stipulating ever lower emission limits. Take the EU, which in 2007 decided to bundle various regulations into one. This resulted in the Industrial Emissions Directive 2010/75/EU, which required member states to set limits for the emission of, for example, oxides of nitrogen (NOx) and carbon monoxide and transpose them into national law. Then in 2017, the EU implemented decision 2017/1442 to establish “best available techniques” (BAT) under the 2010 directive. The consequences? It puts an almost automatic mechanism in place, whereby advances in emission-reducing technologies are regularly evaluated and, where reasonable, lower limits set in legislation and reference documents.
Emission limits: getting stricter all the time
Some EU countries had already started to go down this path before the BAT mechanism was put in place. While the Industrial Emissions Directive determined a limit to be set for gas turbines of 90 mg/m3 for NOx, Germany immediately set a lower threshold of 50 mg/m3 when it implemented the directive in 2013, and further reduced the limit to 40 mg/m3 in 2021.
Germany’s limits for carbon monoxide have remained at 100 mg/m3 for gas turbines. However, operators already have a strong cost incentive to lower their CO emissions as high values indicate that there remains unused potential to generate more electricity.
Being able to somehow measure gases at lower concentrations is not enough for regulatory compliance. In many countries, certification is necessary.
EN 14181, applicable in much of Europe, states that continuous emission monitoring systems (CEMS) must be certified to have passed a QAL 1 qualification test covering the complete system, including its gas paths and conditioning devices. Testing is performed according to EN 15267-3 by an independent accredited authority.
In China, a China Certification for Environmental Products (CCEP) certification is required, whereas for plants in the USA, manufacturers must give a declaration of conformity with EPA guidelines.
Low measuring ranges vs. investment costs
The trend towards lower emission limits is set to continue, making it challenging for operators of gas analysers to strike the right balance between equipping themselves for future requirements and keeping down investment costs, as continuous gas analysers with low measuring ranges tend to be expensive. Recent improvements in the NDIR measurement chamber of the well-established Ultramat 23 continuous gas analyser lets operators have it both ways.
EN 15267-3 and CCEP certified measuring ranges of 0 to 50 mg/m3 for CO and NOx mean that gas turbines can use the instrument to measure these gases down to 20 mg/m3, which is well below current legal limits. These are unprecedentedly low values for a gas analyser of its class. Only high-end analysers have had these capabilities so far.
Monitoring the relevant gases with a single analyser
The Ultramat 23’s highly sensitive CO and NOx measuring capabilities can be applied to two of up to four gases it is able to simultaneously measure around the clock, with a choice of detection methods and sensors.
Its IR detector can be applied to up to three infrared-sensitive gases, and a UV photometer to even smaller concentrations of SO2 and NO2.
For waste incineration and large coal-fired combustion plant applications the Ultramat 23 has received EN 15267-3 certification to determine CO, NOx, NO, NO2, SO2, CO2 and, either paramagnetically or electrochemically, O2.
A further feature usually only available in high-end gas analysers is that day-to-day autocalibration can be performed with ambient air. This saves effort and costs because a test using calibration gases is necessary only once a year.
Mutually exclusive requirements? Not anymore
For large combustion and waste incineration plants, finding the right solution to measure emission gases can be challenging. While budgets for investment in gas analysis equipment tend to be limited, there is a need to be fully prepared for stricter emission limits over the equipment lifetime. Technical innovation is proving that affordability and investment security are not necessarily mutually exclusive.
Author: Clemens Barth Product Manager Ultramat23 and Analytical Application Sets, Siemens (barth.clemens@siemens.com)