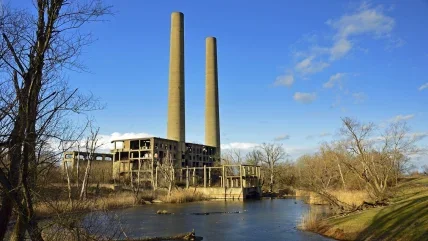
The new combined cycle unit, with an expected commercial operation date of August 2025, will replace the old Awirs power plant complex (originally coal, subsequently employing a range of fuels, including natural gas, oil and biomass). The old plant is in the process of being demolished. The new plant will be a beneficiary of the Belgian capacity remuneration mechanism, introduced in 2021, to help ensure security of electricity supply.
The heat recovery steam generator is the biggest and most efficient ever to be supplied by John Cockerill, and one of the world’s largest HRSGs. As well as the dimensions, other challenges associated with project include very low NOx limits (coupled with very tight ammonia slip controls), use of dissimilar welds (necessary to avoid sensitisation of stainless steel), and stringent acoustic requirements, which have a major impact on the HRSG design.
The new HRSG is being installed downstream of a Siemens Energy SGT5-9000HL gas turbine (593 MWe), achieving a power plant efficiency of over 63%. The power plant will employ a one-on-one multi-shaft configuration, with steam from the HRSG driving an SST5-5000 steam turbine coupled to an SGen5-1200A generator and the HL gas turbine coupled to an SGen5-3000W generator.
A distinguishing feature of the HRSG is its four-module width, with a consequent increase in the number of tubes and heat exchange surface area.
The structural steelwork is enlarged to accommodate the four modules side by side. The casing inside-width is 18.7 m and casing height 26 m. This is the first HRSG of this width, and in terms of these dimensions, the largest HRSG ever. HRSGs for class F and H gas turbines typically employ a three-module width.
Basic data for the HRSG can be summarised as follows:
- Type: horizontal GT exhaust flow, three pressure levels plus reheat (with recovery of heat at the exit of the high pressure ST stage reinjected at the medium pressure level). No duct burner
- Live steam operating conditions at HRSG outlet: HP steam at 602°C and 164 bar; reheat steam at 609°C and 40 bar
- Boiler dimensions: 73 m long; 25 m wide; and stack height 60 m
- Heat exchange surface area: more than 1 000 000 m2, which is a milestone in HRSG evolution
- Number of tubes: more than 27 000, each 26 m long, also a milestone
- Weight: 10 500 t
- Tube materials: hottest superheater and reheater tubes will employ austenitic stainless steel finned tubes in SA 213 Super 304, with Incoloy transitions to ferritic alloy steel outlet headers in SA 335 P92, which is also used for the main steam piping to the steam turbine
- Integrated SCR achieving reduced NOx with low residual ammonia. Requirements (at the stack): less than 10 mg/Nm3 NOx; max NH3 slip 1.5 mg/Nm3
- CFD modelling performed for the SGT5-9000HL has demonstrated that there is no need for an attenuation flow grid in the HRSG inlet duct thanks to the long transition duct between GT exhaust and HRSG inlet. This long straight duct is just a provision for the potential future addition of a bypass stack
Despite the high HP pressure, the HRSG is of the conventional drum type, and is perhaps at the limit for this technology, because of water/ steam separation limitation in drum demisters. To achieve higher pressures, a once through boiler (OTB) configuration would be preferable for the HP circuit, and indeed John Cockerill is currently noting a market shift towards OTB technology to accommodate the largest gas turbines. A vertical-flow OTB, manufactured by Siemens/NEM, is employed at the Keadby 2 HL lead CCGT project in the UK.
Boiler Stress Evaluator software (based on Euro Norm codes), developed by John Cockerill, will be uploaded into the Flémalle power plant DCS and combined with dedicated temperature measurements on critical components such as the outlet headers and HP drum. This will enable boiler lifetime to be monitored and support predictive maintenance. Thermocouples will provide temperature profiles over the thick walls during transients, and induced thermal stresses will be calculated.
The order for the Flémalle HRSG was placed at the end of 2022 and site erection work is expected to start at the end of 2023.
The new combined cycle plant will be highly flexible in operation. “Designed to facilitate frequent start-ups and changes of regime, it will also provide all the flexibility necessary to adapt to the significant production fluctuations required by the intermittent side of renewable energies”, says Eric Absil, president of John Cockerill Energy Solutions, noting that in the current context of the energy transition, combined cycle power plants are “a key element of national energy mixes.”
Gilian Deblauwe, managing director, ENGIE Thermal Cluster North Europe, says his company has “made great efforts to develop a state-of-the-art project in Flémalle in order to reduce the impact on the environment and to integrate the plant into local communities”, and “decided to go beyond its obligations by further reducing NOx emissions… We are convinced that the Flémalle plant, which represents an investment of 500 million euros, will be one of the world’s best benchmarks in terms of efficiency and emissions control.”
ENGIE subsidiary Electrabel is acting as EPCM contractor for the Flémalle combined cycle plant and has thus contracted with John Cockerill for the HRSG package, which includes balance of plant portion and pipe rack to steam turbine building, and also HRSG erection activity.
John Cockerill has previously worked with ENGIE on the supply of heat recovery steam generators for combined cycle power plants, at Amercoeur (Hainaut, Belgium) and Dunamenti (Hungary).