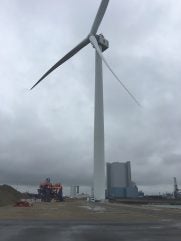
Since the birth of the world’s first electricity producing wind turbines towards the end of the 19th century, it took a full century before the first offshore wind farm was constructed, off the coast of Denmark in 1991. The Vindeby wind farm featured 11 turbines with a generating capacity of 450 kW each. By the time the first offshore wind farm was installed in UK waters less than a decade later it was using 2 MW machines and since then turbine capacities have accelerated rapidly.
The Chinese have recently announced production of a 26 MW wind turbine, while Western companies have standardised their commercial offerings around the 15 MW mark.
These machines are veritable titans. The Vestas V236-15.0 MW turbine, for example, features 115.5 m long blades, Siemens Gamesa has its SG 14-236 DD 15 MW with a rotor diameter of 236 metres, while the biggest of the Haliade-X machines from GE has a rated capacity of 14 MW and a 220 m diameter rotor. The huge torque generated by a 200 m+ rotor has prompted fundamental changes in turbine design. For instance, the largest machines typically feature direct drive technology in which the rotor is connected directly to a permanent magnet generator. This design eliminates potential failure points, such as a gearbox that might otherwise be necessary, but also allows the top head mass of these machines to be kept as low as possible and the nacelle to remain relatively compact. This supports easier transportation and installation, as well as good engineering, but these design principles also introduce several challenges.
NREL’s 2020 definition of the IEA 15 MW reference offshore wind turbine uses a direct drive layout with a permanent-magnet, synchronous, radial flux outer-rotor generator in which the air gap between the rotor and stator is assumed to be 1/1000th of the 10.53 m air gap diameter. The air gap is thus around a nominal 1 cm, while in the reference model, a 20% deflection is allowed to accommodate for the influence of the support structure, drive shaft, and turret. With a generator efficiency of 97% in a 15 MW machine around 450 kW of heat needs to be efficiently removed through the 1 cm gap between the stationary and rotating elements of the generator. It’s clear then that one of the big problems associated with the largest offshore wind turbines – housed in a compact box and facing significant weight restrictions – is actually cooling.
To deliver the necessary cooling capacity, turbine designers have introduced the concept of forced air or direct air cooling in which a large, ducted fan is used to suck ambient air through the generator to remove excess heat. But, while this solves the cooling problem, pulling large volumes of ambient air through complex electrical machinery also introduces additional challenges too. In particular, it introduces new requirements for effective air filtration.
A new kind of turbine demands new filtration
Given this new class of wind machines are packed with cutting-edge technology they share many parallels with today’s advanced gas turbines. Both represent highly demanding applications, depend on operating to higher tolerances than previous generations, and both are extremely high value assets. Both classes of machine also require the highest levels of protection. Gas turbines are subject to airborne fouling, erosion and corrosion of blades that can catastrophically impact efficiency. The performance of wind turbines can also be negatively impacted in a similar way. One of the most pernicious contaminants for offshore wind turbines is salt water. This complex material is notoriously difficult to manage given it can penetrate deep within a machine, change phase, combine with other contaminants and can rapidly accelerate corrosion, which is a notable concern for the latest generation of offshore machines.
However, while salt is a key issue for offshore wind turbines, dust and particulates, insects, and even birds can all potentially become problematic if they find their way into the nacelle and the delicate equipment within. Under these circumstances, having optimal air filtration, with higher particulate, salt and liquid removal becomes critical. Rather like the gas turbines found on offshore drilling rigs or aboard naval vessels, many of the primary considerations for wind turbine air filtration are the same, given the salty and humid environment. Any filtration system must protect the machine from the ingress of corrosive materials like salt and water, as well as dust and other kinds of contaminants. Removing particulates substantially reduces the possibility of salt leaching or becoming re-entrained in the air stream for example. At the same time, the filtration system must be as compact as possible and also perform its core function while producing minimal differential pressure across the filter elements. Pressure loss characteristics can have multiple negative implications in terms of issues like parasitic power demand from the fan-forced air flow as well as the eventual size of the fan needed to deliver the necessary volumes of air. A larger fan not only adds to capital costs and top head mass but also takes up valuable and limited space in the nacelle. A factor uniquely important to offshore wind applications is also the lifespan of the filter elements. Extended filter life is particularly important given difficulties and extreme costs associated with accessing and servicing an offshore machine.
Balancing these – often competing – demands requires profound understanding of aerodynamics, filtration media and manufacturing, as well as the ambient environment and how it changes seasonally.
Building on gas turbine experience
Known for their role in supporting gas turbine operations, air filtration experts Parker Hannifin have also been a leading supplier of filtration systems to naval vessels since the 1960s. For instance, the Parker Hannifin Altair Neptune filtration system uses a three-stage approach designed to remove both solid and liquid contaminants in all weather conditions and at all levels of humidity. With an unequalled pedigree supplying high-velocity compact filtration solutions in the marine environment for military applications, as well as for gas turbines in demanding service roles in offshore and coastal oil and gas environments, Parker Hannifin was ideally placed to partner with a major wind turbine OEM to develop an appropriately rigorous and robust air inlet filtration system. With a mission to optimise the aerodynamics in as small a package as possible while also balancing that with pressure loss and filter life span, Parker Hannifin established a three-year development programme working with the manufacturer, including the development of a dedicated test rig and a two-year on-site testing scheme on a working prototype turbine in Rotterdam.
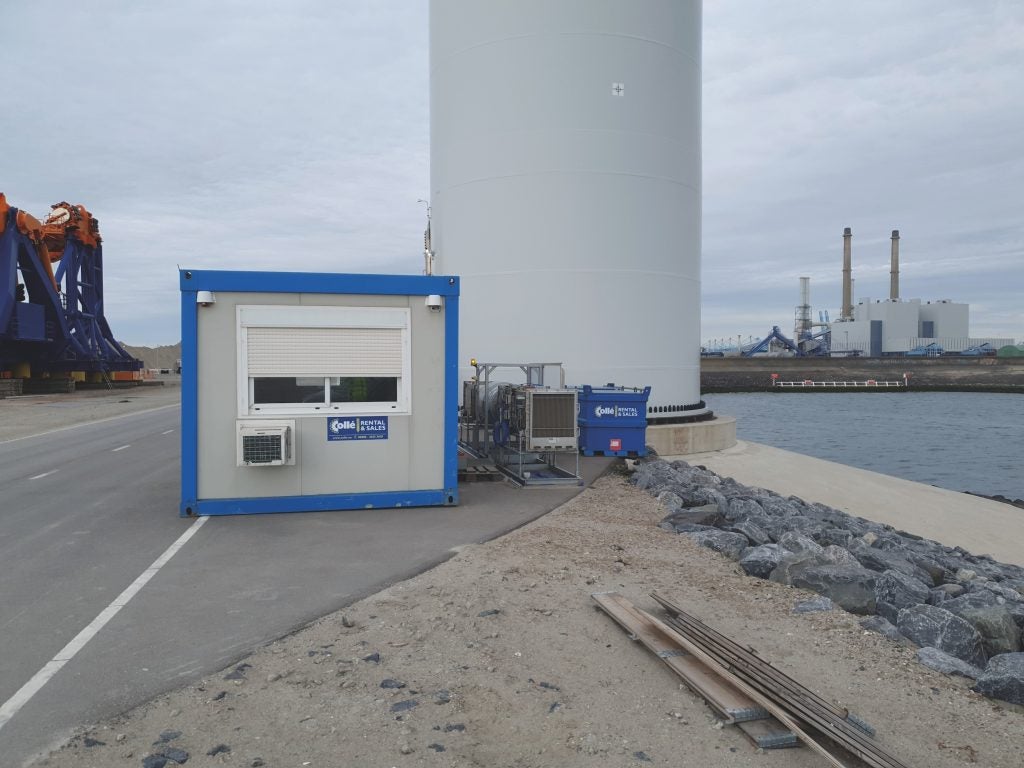
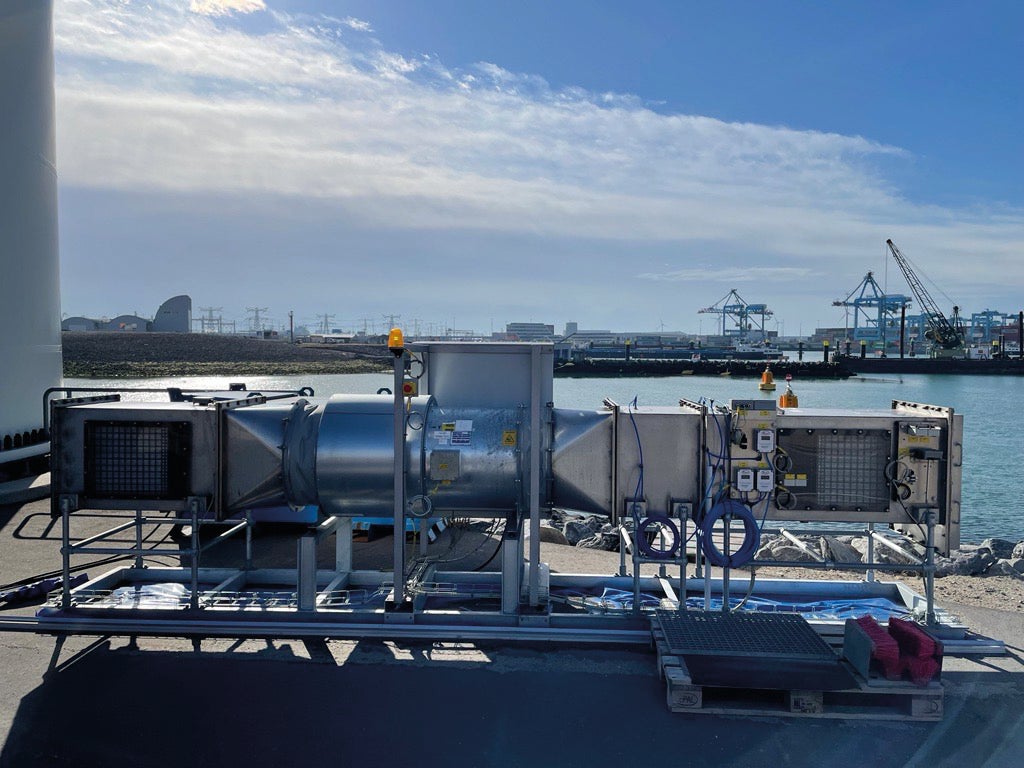
Parker remote air filtration test facility at Rotterdam
14 MW wind turbine test site
Comprehensive testing of the filtration systems measured salt and corrosion upstream and downstream among many other parameters and resulted in a Parker Hannifin product validated for service in the largest wind turbines.
Rated at F9 (EN779:2012) and T9 (ISO 29461), high efficiency filtration, the engineered solution was a two-stage system with an inertial vane separator that prevents liquids like rain or spray and large objects from entering the innards of the filtration system. Essentially, a highly aerodynamically optimised inertial louvre system, this causes the air flow to change direction several times, shedding its larger sized liquid droplets. Downstream of that is installed the high efficiency hydrophobic final filter consisting of pleated glass fibre media with extended surface area for long operational life, which removes any remaining liquid and in particular salt solutions.
The cleaned air is then free to pass through the nacelle, cooling the generator, bearings and internal electronics. Remarkably, the system offers a four-year lifespan when deployed in locations such as the North Sea or the Atlantic coast off North America. In part, this is due to the relatively low particulate loading found at the 300 m height of an offshore wind turbine nacelle, although it is important to note that higher particulate removal filters, EPA (EN1822) grades E10-E12, could be installed if operators consider it important to deliver even cleaner air – but this may come at the cost of some filter lifespan.
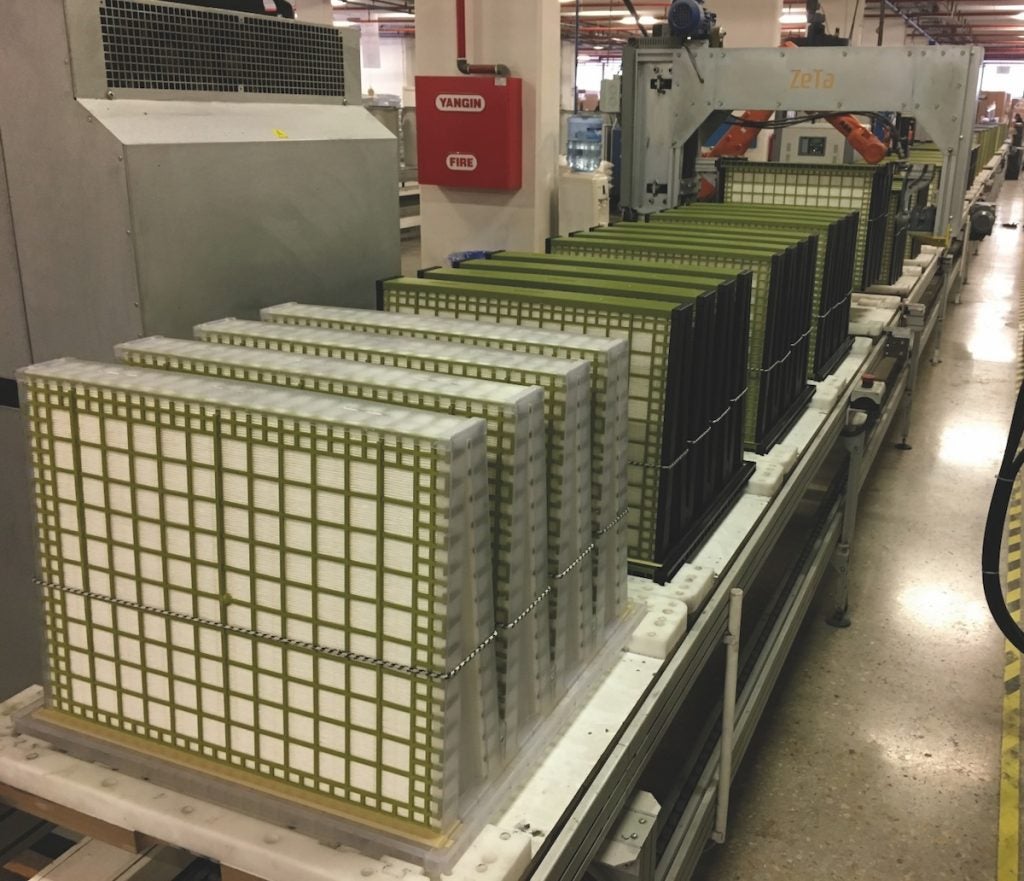
This wind turbine filtration system has emerged from Parker Hannifin’s experience in the gas turbine world where compact and high-velocity filtration is a necessary element but also benefits from in-depth testing and an R&D programme that has seen test rigs installed all over the world in all sorts of different environments to ensure functionality wherever these large turbines are ultimately deployed. There they will serve to address corrosion concerns to ensure a long asset service life while also providing the necessary longevity to keep servicing costs to a minimum, all in a compact and lightweight package.
The next generation of large wind turbines requires the same level of protection as an advanced gas turbine and for exactly the same reasons. They are the sensitive thoroughbreds of the energy sector and demand the highest standards of air inlet filtration.