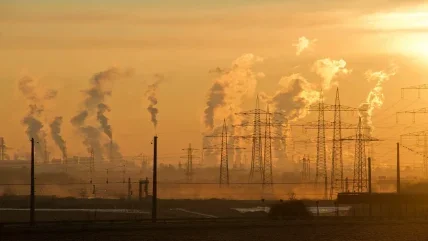
The supercritical CO2 (sCO2) cycle is a closed, recuperated heat engine cycle with the working fluid state-points (partially or wholly) above the critical point of carbon dioxide (73.8 bar and 31.1°C). If the heat rejection part of the cycle is in the supercritical region, it is referred to as sCO2 Brayton cycle. If the heat rejection part of the cycle is below the critical point and entails condensation of CO2, it is referred to as sCO2 Rankine cycle. Its emergence as a potential rival to the conventional steam Rankine cycle for electric power generation can be traced to the late 1960s. A key modification to the recuperated cycle is splitting the hot CO2 flow downstream of the recuperator to enable reduced cycle heat rejection for higher efficiency. At present, this is the most widely investigated sCO2 cycle variant – known as the “part-“ or “split-flow” re-compression cycle – with a cycle pressure ratio (PR) of about 3:1 and cycle maximum temperatures up to 760°C.
A further modification of the simple recuperated cycle, known as partial cooling, entails the addition of a pre-cooler and pre-compressor upstream of the re-compressor. Flow split takes place at the discharge of the pre-compressor. The net effect of the pre-cooler and pre-compressor is to reduce the temperature of sCO2 at the discharge of the re-compressor. One effect of this modification is to increase the temperature range of the cycle heat addition, which makes it more suitable to a bottoming cycle, ie, heat recovery applications. The other effect of the partial cooling modification is an increase in cycle PR, from 3:1 to about 4:1 by enabling lower turbine exhaust pressure. Overall, though, everything else being the same, split-flow re-compression has comparable efficiency but the partial cooling cycle boosts plant net output significantly.
Until the early 2000s, sCO2 power cycle technology was dormant due to limited availability of and/or experience with high temperature–pressure materials and high-performance heat exchangers (with low pressure loss and high effectiveness, ie, above 95%) requisite for acceptable cycle efficiency with low cycle PR. Since then, there has been a veritable renaissance in sCO2 power generation cycles for applications including nuclear, concentrated solar, fossil-fired (coal and natural gas), and waste heat recovery. So far, the experience has been limited to small-scale pilot and/or demonstration facilities with indirect heat addition (ie, no combustion, fully closed cycle).
The most intriguing application of sCO2 technology is the semi-closed variant with direct heat addition via oxycombustion, utilising natural gas or syngas (generated by gasification). Two early variants of oxycombustion cycles were the Graz and Matiant cycles, which did not proceed beyond paper concepts. The Matiant cycle is the more cumbersome of the two and comprises an sCO2 Rankine cycle combined with a regenerative CO2 Brayton cycle with reheat. The Graz cycle is simpler in that it is similar in basic construction to the simple recuperation sCO2 cycle. Combustion products consisting of CO2 and H2O are expanded in a turbine, followed by a condenser where steam is condensed and CO2 is vented, compressed, and transported to a site for utilisation or sequestration. Condensate is pumped and recycled to the combustor where
it acts as the moderator in the stoichiometric combustion process with O2. Another version of the Graz cycle was the basis for a demo plant with a General Electric J79 turbine, minus the compressor, to be driven directly by a 170 MWt high-pressure, oxycombustor.
Allam–Fetvedt Cycle
A variation of the cycles described above, sometimes referred to as water cycles because of recycled H2O used as combustion moderator, is the Allam cycle, where the combustion moderator is recycled CO2 at 300 bar. In the Allam cycle, CO2 constitutes (nominally) 95% of the fluid flow in the combustor (by mass) with the rest, 5%, made up of oxygen and fuel. The resulting combustion product is roughly 90%(v) CO2. Oxygen for combustion is generated by a cryogenic air separation unit (ASU). Carbon dioxide generated by the combustion is taken away from the cycle at the condenser discharge to maintain the cycle mass balance (hence semi-closed). After the condenser with H2O removal, the CO2 content of the recycled working fluid is 97%(v) CO2. A simplified schematic of the semi-closed Allam cycle is shown in Figure 1. Eliminating the ASU and replacing the combustor with a heat exchanger, the cycle configuration is identical to a conventional, simple recuperated (closed) sCO2 cycle.
Developers of the technology (NET Power now in partnership with Baker Hughes) have made announcements about potential zero-carbon projects consisting of 300 MWe commercial power plants based on what they now refer to as the Allam–Fetvedt Cycle (AFC). A recently announced project is a plan to develop and build a “utility-scale natural gas-fired power plant with near-zero atmospheric emissions” at an Occidental hosted site near Odessa, Texas, “expected to be on line in 2026”, with Constellation Energy in the role of plant operator and power off-taker.
The Allam cycle has received significant attention over the past decade. A 50 MWt test facility in La Porte, Texas, was built and operated to demonstrate the oxy-fuel combustor and the turbine. A press release in late 2021 stated that the Allam cycle turbine at La Porte had delivered electricity to the ERCOT grid.
According to a presentation given by NET Power at the International sCO2 Power Cycles Symposium, 21-24 February 2022, San Antonio, Texas (where the author gave a keynote address), 900 fired hours at 300 bar and about 1000°C turbine inlet temperature was achieved at LaPorte. The unit was synchronised to the ERCOT grid with stable and controlled ramp and shutdown. In addition, the operation of the compact heat exchanger (the recuperator) constructed with a nickel-based alloy was also demonstrated. NET Power also reported that a number of commercial scale projects were under development and a pre-FEED study for a 284 MWe plant had been completed.
The inherent carbon capture capabilities of the oxycombustion sCO2 cycle (ie, without a complex and costly chemical process plant add-on) with (advertised) 59% net LHV efficiency has created a unique aura around this simple yet powerful zero-carbon power plant concept.
Although not mentioned at the International sCO2 Power Cycles Symposium, the study report for the Whitetail project in the UK, prepared by 8 Rivers (owner of the AFC technology) and including a study by McDermott, can be found online. The design and configuration of the AFC Whitetail plant does not include a dedicated ASU to generate the oxygen for combustion, which is supplied via a pipeline from another facility. The heat shown as being provided by the ASU in Figure 1 is produced by a dedicated hot gas compressor (HGC), equipped with a 60 MWe electric motor. While the standard AFC cycle is based on 1150°C turbine inlet temperature, this was deemed risky for the first plant. Thus, the report includes a design for a base case at 900°C turbine inlet temperature and an alternative case at 925°C for the UK standard plant (see Table 1). Without heat integration, ASU power consumption is roughly 10% of the cycle fuel consumption (no heat integration with the power cycle), which comes to about 57 MWe, confirming the trade-off with the HGC.
Liquid oxygen (LOX) storage can be incorporated into the AFC. In this concept, the ASU is operated during times of low demand (low or negative electricity price) at full load or part load (depending on the price) and the stored LOX is used during periods of high demand and electricity price. Not utilising the ASU during operation with stored LOX can increase the net plant output by 20%. Another energy storage option is combining green hydrogen (via electrolysis) with the AFC by burning the stored H2 in the oxy-combustor (with or without LOX storage).
Pumped thermal energy storage cycles As reported at the February 2022 International sCO2 Power Cycles Symposium, sCO2 power cycles are being developed for both indirect and direct cycle heat addition (fired) configurations, including those for energy storage. Examples of the latter include the trans-critical CO2 cycle and other pumped thermal energy storage (PTES) cycles developed by Echogen, GE, and MAN/ABB.
The basic operating principle of PTES cycles is illustrated in Figure 2. For simplicity, only one turbomachine operating on a simple Brayton cycle is depicted in the diagram. During the charge mode, the system runs as a closed cycle heat pump (or refrigerator, depending on your objective, ie, heating or cooling) in a reverse Brayton cycle, receiving heat from a cold reservoir and rejecting it to a hot reservoir. (This is why the technology is referred to as pumped TES.) During the discharge mode, the system runs as a closed cycle gas turbine in a Brayton cycle, receiving heat from a hot reservoir and rejecting it to the cold reservoir.
In practice, there are two turbomachines, a reverse Brayton cycle heat pump driven by an electric motor and a Brayton cycle gas turbine driving an electric generator. For maximum efficiency, both cycles incorporate recuperation, to heat (cool) compressed working fluid in the gas turbine (heat pump). The hot reservoir comprises two storage tanks for the TES medium, eg, molten salt or another suitable heat transfer fluid. Similarly, the cold reservoir also comprises two tanks for storing the cold medium, typically water/ice (sometimes mixed with a suitable liquid, eg, methanol). In the TES heat pump technology developed by Malta, the working fluid of the heat pump and gas turbine cycles is air. In the trans-critical CO2 cycle, the CO2 working fluid goes through both subcritical (ie, the heat pump evaporator) and supercritical states, hence the moniker trans-critical. In the PTES system developed by GE, sCO2 is the working fluid of the heat pump with molten salt thermal storage (up to 480°C). Electric resistive heating is used to heat the molten salt to 565°C. The discharge cycle uses a standard Rankine cycle with water/steam as the working fluid. The cold storage medium is water. MAN/ ABB Electro-Thermal Energy Storage (ETES) utilises ice for cold storage and hot water for hot storage. Both turbomachines operate in sCO2 cycle. Expected roundtrip efficiency (RTE) of pretty much all the PTES systems under development is around 60%.
Molten salt based TES can be combined with an sCO2 power cycle in concentrated solar power (CSP) applications. This is the technology promoted by Heliogen, with turbomachinery developed by Hanwha and tested at Southwest Research Institute. The initial commercial offering is a 5 MWe system with 600°C turbine inlet temperature operating in a split-flow (re-compression Brayton Cycle). Targeted deployment date is early 2024.
Another interesting technology for CSP applications is thermochemical energy storage (TCES), which is being investigated by GE’s Global Research Center (under the ARPA-E FOCUS programme) and Echogen (under the ARPA-E DAYS programme). The goal is to combine TCES with TES, which uses the excess solar energy and stores it in molten salt. The excess energy from the grid is used to cool liquid CO2 to solid (dry ice) and release the heat from the molten salt to change solid CO2 to supercritical fluid and expand it in a turbine. Targeted RTE is 68%.
SunShot and STEP
There has been no sustained field experience yet with sCO2 turbines or power plants. The first attempt to design and operate a larger-than-laboratory scale demo/test was the Advanced Projects Offering Low LCOE Opportunities (APOLLO) project under the aegis of the US DOE’s SunShot initiative. The project was a collaboration between GE and SwRI to develop a high-efficiency sCO2 compression system (80% compressor efficiency with variable IGVs and OGVs). The compression system in question comprised two compressors, the main compressor and the re-compressor of the split re-compression sCO2 cycle, each rated at 2 MW.
The system was intended as a modular power block for CSP applications. The powertrain (27 000 rpm) also comprises a 14 MW four-stage sCO2 expander for net 10 MW (rated) generator output. Turbine inlet conditions were 715°C and 250 bar with about 85 kg/s sCO2 flow rate. The work under the SunShot initiative encompassed six years (2012-2018), achieving considerable success and providing a wealth of lessons learned for next steps, notably, a 10 MWe, $119 million sCO2 pilot plant facility, which, at the time of writing, is under construction on the campus of Southwest Research Institute, San Antonio, TX, USA.
The project is being undertaken under the US DOE’s Supercritical CO2 Transformational Electric Power (STEP) programme (with the US DOE footing $84 million of the bill). A team led by GTI Energy, SwRI and GE was established to design, construct, commission, and operate the facility. The project goal is to advance the state-of-the-art for the high temperature sCO2 power cycle from TRL 3 to TRL 7.
The STEP turbine skid is shown in Figure 3.
The three-stage STEP turbine is designed to incorporate improvements on the SunShot unit, eg, increased casing and rotor life (100 000 hours vs 20 000 hours), shear ring retention rather than bolts, a design for couplings on both shaft ends, and improved aero performance with increased volute flow area (see Figures 4 and 5). Special attention is given to the dry gas seal (DGS) design and thermal management based on the lessons learned from the APOLLO (SunShot) projects.
The test programme is divided into two phases. In Phase I, a simple recuperated variant will be operated to demonstrate 500°C turbine inlet temperature operation with reduced risk. In Phase II, the split-flow (re-compression) cycle with parallel compressors and multiple heat exchangers will be deployed to operate at 715°C turbine inlet temperature operation with maximum efficiency. The announced goal is to demonstrate the pathway to 50% or higher efficiency. Since the heat source of the STEP facility is a natural gas fired heater (similar to a heat recovery steam generator in construction), the efficiency measured in the tests will be significantly lower than 50%.
Ongoing research
Achieving 50% or higher net LHV efficiency in a power plant operating in sCO2 Brayton (or Rankine) cycle pushes technology to the limits in turbo machinery, heat exchangers, seals, and bearings.
In addition to already mentioned R&D activities under the aegis of the US DOE (eg, the STEP facility), OEMs such as GE, Siemens, Hanwha, and others are also active in product development. Offices and national laboratories of the US Department of Energy are active in investigating applications of the sCO2 cycle to CSP and nuclear energy. Fundamental research is being conducted in university labs on combustion, aerodynamics, and heat transfer areas pertinent to sCO2 cycle components. As an example, one can cite the falling particle central receiver concept investigated by the Sandia National Laboratories. The goal is to achieve high turbine inlet temperature (up to 1000°C) in CSP applications, for higher cycle efficiency. (When using the molten salt as heat transfer and energy storage medium, the upper temperature limit is about 560°C.)
To achieve the highest possible cycle efficiency, effective heat transfer with low pressure loss in the recuperator is a must (ie, higher than 95% effectiveness with less than 2% pressure loss in hot and cold legs). This requires complex heat exchanger designs, ie, printed circuit (PCHE) or plate-and-frame (PFHE), with parts made from nickel-based alloys or other materials (aluminium or stainless steel). Construction of such complex components requires advanced subtractive or additive manufacturing techniques such as laser cutting/welding, 3D printing, electrochemical machining (ECM), and electro discharge machining (EDM). (Note that the STEP turbine rotor is fabricated using a 5-axis EDM machine.)
A particular concern is maintaining the integrity of parts under thermal stresses caused by normal operating transients such as startup, shutdown, and load ramps. This will be one of the key focus areas in the STEP programme (with PCHE recuperators designed and manufactured by Heatric).
A novel technology under development by GE is trifurcating heat exchangers manufactured via direct metal laser melting (DMLM) using GE AM303 superalloy or binder jet 3D printing (employing SS316L). The trifurcating geometry is claimed to achieve twice the power density of conventional designs. DMLM technology (at a TRL of 4) with superalloy materials enables up to 900°C turbine inlet temperature at 250 bar with less than 0.5% pressure loss.
Accurate property calculation, especially with the presence of impurities in the sCO2 working fluid, is of prime importance for performance prediction and trouble-free operation of sCO2 cycle equipment. Potential problems include significant shift in the operating point and corrosion. Elimination of these risks requires extensive operation and data collection over the entire operating map of the compressors and the turbine. The STEP test campaign will be a huge step in sCO2 technology advancement in this respect.
Thermodynamics perspective
All heat engine cycles are attempts (in many cases, quite feeble) to approach the theoretical ultimate, ie, the Carnot cycle. According to the Kelvin–Planck statement of the second law of thermodynamics, there can be no heat engine operating in a cycle more efficient than a Carnot cycle operating between the same temperature reservoirs (ie, maximum and minimum cycle temperatures, TMAX and TMIN, respectively). In practice, this is an impossible feat to accomplish. Conventional Brayton (gas turbine) and Rankine (steam turbine) cycles are indeed far removed from the Carnot ideal. In simple terms, their mean-effective cycle heat addition and/or heat rejection temperatures (henceforth, METH and METL, respectively) are well short of TMAX and TMIN (in the case of the Brayton cycle, both). Attempts to address these problems, ie, to Carnotise the heat engine cycles, usually involve several thermodynamic ‘tricks’, eg, intercooled compression (to approximate isothermal heat rejection), recuperation (to increase METH and to reduce METL, simultaneously), and/or reheat (to approximate isothermal heat addition). Supercritical CO2 cycles with recuperation and intercooled compression (combined with pumping in latter stages) are effectively Carnotised Brayton or Rankine cycles.
The temperature–entropy (T–s) diagram of the intercooled-recuperated sCO2 cycle in Figure 1 is shown (in a generic manner) in Figure 6.AsshowninFigure6,T4=TMAX,andT1= TMIN, which is usually assumed to be 15°C (ISO ambient temperature). The ideal cycle performance can be calculated using the air-standard cycle approach, ie, (i) ideal gas equation of state, (ii) constant specific heat, cp (ie, perfect gas), and (iii) perfect recuperation, ie, T3 = T5 and T2 = T6. METH is the logarithmic average of T3 and T4 = TMAX, and easy to evaluate. Calculation of METL requires tedious enthalpy/entropy change evaluations for pre-cooling, inter- and after-cooling. (For the AFC, METL ~ 317°C.) Consequently, assuming perfect (isothermal) compression, with METL ~ TMIN = 288 K suffices for a conservative estimate.
Ideal cycle calculations with specific heat ratio γ = 1.18 are shown in Figure 7. Mature technology (plant basis) performance is estimated using a technology factor (TF) of 0.75. This is comparable with the rating performances of modern gas turbine combined cycles with advanced H/J class machines (turbine inlet temperature close to 1700°C with cycle PR in the range 24:1 to 25:1).
It should be noted that this performance level took close to a half century to achieve after the technology was already at TRL = 9.
The next steps
Considerable R&D investment in sCO2 technology continues. The STEP facility, due to enter the operational phase in late 2023, is expected to make a strong contribution to the advancement of the technology, which is still far from reaching the coveted TRL of 9.
The oxy-combustion variant (notable the Allam–Fetvedt Cycle) with inherent CO2 capture capability is potentially a worthy competitor to, say, advanced class GTCC with post-combustion capture. The latter is readily capable of 51% net LHV efficiency with mature technology today (eg, capture employing chemical absorption with generic amines).
Even so, recent field experience should make one cautious that even with readily available technologies successful deployment of new applications takes a long time until all the bugs are ironed out and performance potential is fulfilled.
As far as CSP and industrial waste heat recovery applications are concerned, sCO2 is indeed a strong contender relative to, say, organic Rankine or small steam Rankine cycles. Upon the successful completion of the STEP test campaign, the only remaining hurdle will be cost-effectiveness.
Author: S. Can (John) Gulen Bechtel Fellow, Bechtel Infrastructure & Power, Inc