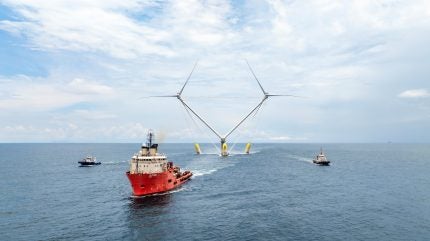
On 13 August Minyang’s OceanX, at this time the world’s largest single capacity floating wind power platform, completed its journey from Guangzhou to the Yangjiang Mingyang Qingzhou IV offshore wind farm in Guangdong province, China, a 191 nautical mile, 50 hour voyage.
Developed by Mingyang Group, this floating wind turbine platform is arranged in a ‘V’ shape and carries two 8.3 MW turbines. With its total capacity of 16.6 MW, it can be used in a wide range of sea areas around the world even at water depths greater than 35 metres. The OceanX blades rise to 219 metres at the highest point, while the whole wind turbine platform has a displacement of 15 000 tonnes and a towing draft of 5.5 m. Once operational, it is expected to produce 54 million kWh annually.
OceanX is said to advance wind turbine innovation by enhancing core component technology, driving both aesthetic and functional refinement in design and manufacturing. Unlike traditional floating foundations, OceanX’s foundation consists of three floats, concrete arms and connectors. It pioneers the use of ultra-high performance concrete with a compressive strength exceeding 115 MPa for a floating construction, a material 4 times stronger than standard concrete, significantly enhancing load-bearing capacity. The foundation also utilises a pre-stressed high-strength concrete assembly structure, which is said to facilitate modular and batched manufacturing, thereby substantially reducing construction costs. Mingyang has utilised caisson pre-tensioning technology in its precast concrete construction, emphasising interface sealing and the precision of the pre-stressing process. With 1500 steel strands threaded through the floating body’s arm, it has good control of tensioning forces and ensures uniform stress throughout the construction. OceanX also introduces what its maker says is cutting edge float design, using layered material to replace traditional steel or hybrid materials. The design lightens the floats and accommodates their curved form. The three streamlined ellipsoidal floats offer reduced wave resistance and enable lateral rotation, providing yawing power. Rigorous testing confirmed that the streamlined shape strikes an ideal balance between stability and load-bearing. Notably, housing two wind turbines on a single floating platform can significantly cut down the per-kilowatt cost, as well as reducing the required sea area and operational maintenance expenses.
Other design points
OceanX’s tower, with its elongated elliptical design, is intended to maximise wind exposure along its longer axis, significantly exceeding that on the shorter axis. By aligning the tower with the wind direction at an optimal angle, the wind platform’s area is effectively increased, allowing for swifter alignment to the wind and boosting the efficiency of wind energy capture. Also, the towers are fitted with a dual-access system for lifts and ladders, ensuring the safety of personnel. In addition to the evolution of the wind turbine form, Mingyang also expanded the boundaries of the application of the cable-stay system, installing it for the first time globally in a wind turbine. A network of 13 main and 6 auxiliary cables efficiently tensions the mainframe, tower, and floating foundation, establishing a stable tensioning mechanism across the wind turbine’s components. So instead of the tower bearing the full impeller and gravity loads, the system distributes the tower’s gravity load to the tension cables, with the tower now only partially supporting the impeller loads. This strategic redistribution significantly lightens the tower’s load, enabling a streamlined and lightweight structural design.